L’offre alternative de solution électrique
Si l’on pense souvent à la solution des batteries lorsqu’on parle de véhicules électriques, ce n’est pas la seule technologie disponible, ni la plus adaptée à tous les modes et usages des transports.
Le marché de la mobilité est séparé en 2 grands pôles : les véhicules personnels et les véhicules professionnels. L’une des différences entre ces deux modalités est le taux d’utilisation du véhicule, c’est-à-dire le rapport entre le temps d’utilisation réelle du véhicule et le temps total disponible.
Pour les véhicules personnels, ce taux est assez bas. Un jour de semaine classique, le véhicule sera surtout utilisé pour l’aller-retour au travail, avec un long temps d’immobilité entre les deux. Pour ce genre d’usage, le modèle électrique à batterie est bien adapté. En effet, une voiture électrique se caractérise encore par un temps de rechargement assez long, de l’ordre de l’heure à la demi-journée en fonction de la puissance fournie et du type de véhicule.
Dans un usage professionnel, on ne peut se permettre d’immobiliser un véhicule sur un temps aussi long. La batterie ne répond donc pas forcément à cet usage. C’est là qu’intervient une autre modalité électrique : la pile à combustible.
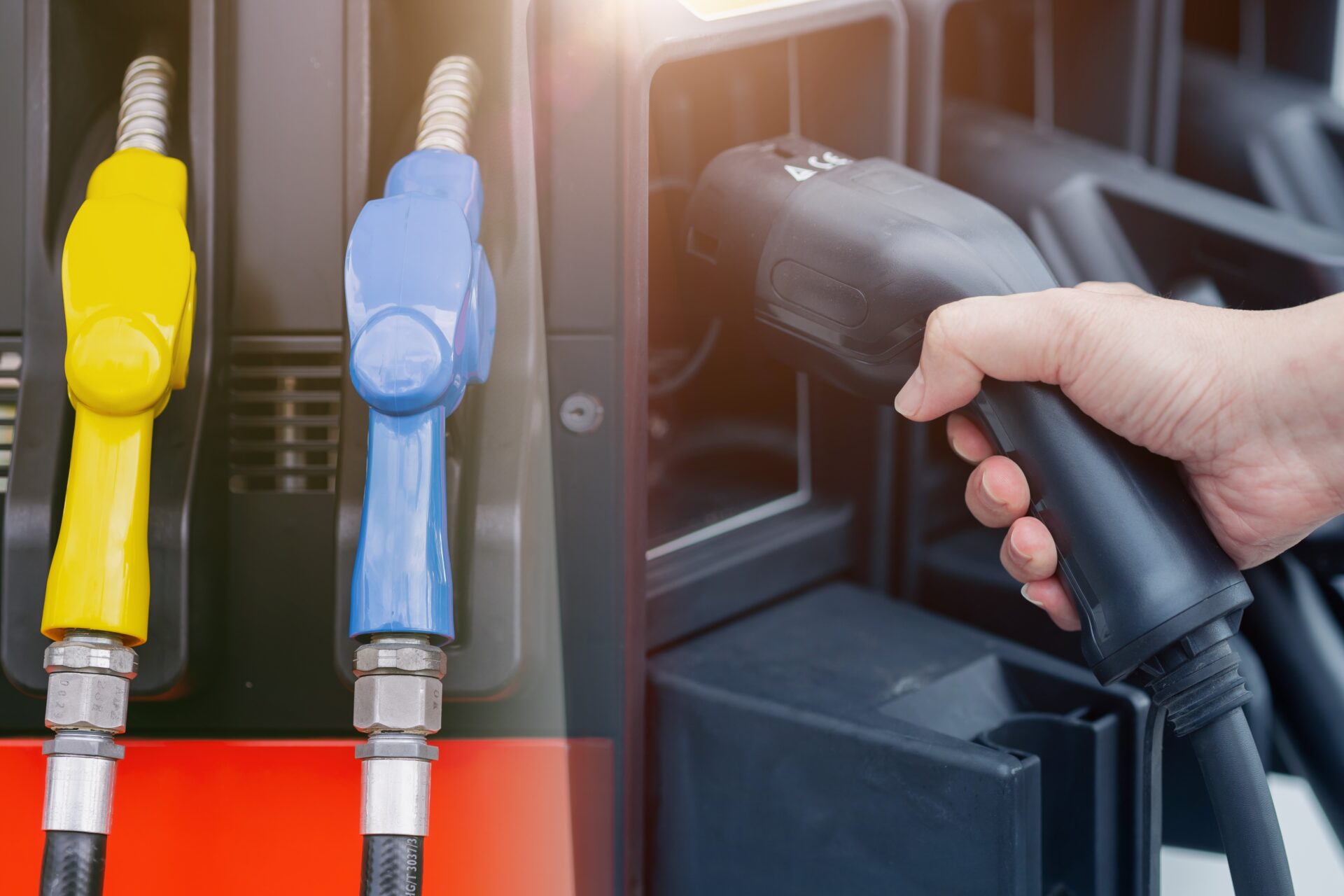
La technologie de pile à combustible
La pile à combustible à membrane échangeuse de protons (PEMFC) permet un fonctionnement " à basse pression et basse température " permettant de les intégrer dans des véhicules. Son principe est simple : injecter de l’hydrogène, le faire réagir avec l’oxygène de l’air et transformer l’énergie chimique de cette réaction en énergie électrique utilisable pour faire avancer le véhicule.
Un véhicule équipé d’une pile à combustible devra donc faire régulièrement le plein en hydrogène afin d’alimenter cette pile. Or, une recharge en hydrogène est bien plus rapide (quelques minutes) que la charge d’une batterie. Elle permet donc un taux d’utilisation du véhicule beaucoup plus élevé, ce qui rend cette technologie particulièrement adaptée à différents véhicules professionnels de transport tels que taxis, navettes, utilitaires, fourgons ou transports lourds de marchandise.
Il existe à l’heure actuelle 9 stations-service à hydrogène pouvant fournir des véhicules équipés de piles à combustible à Paris. En Europe, en 2023, 254 stations existaient déjà et 37 nouvelles étaient ouvertes. La même année, le Parlement européen adoptait officiellement de nouvelles réglementations visant à imposer l’installation de ces stations-service à hydrogène tous les 200 km le long des routes principales de l’Union Européenne d’ici à 2031.
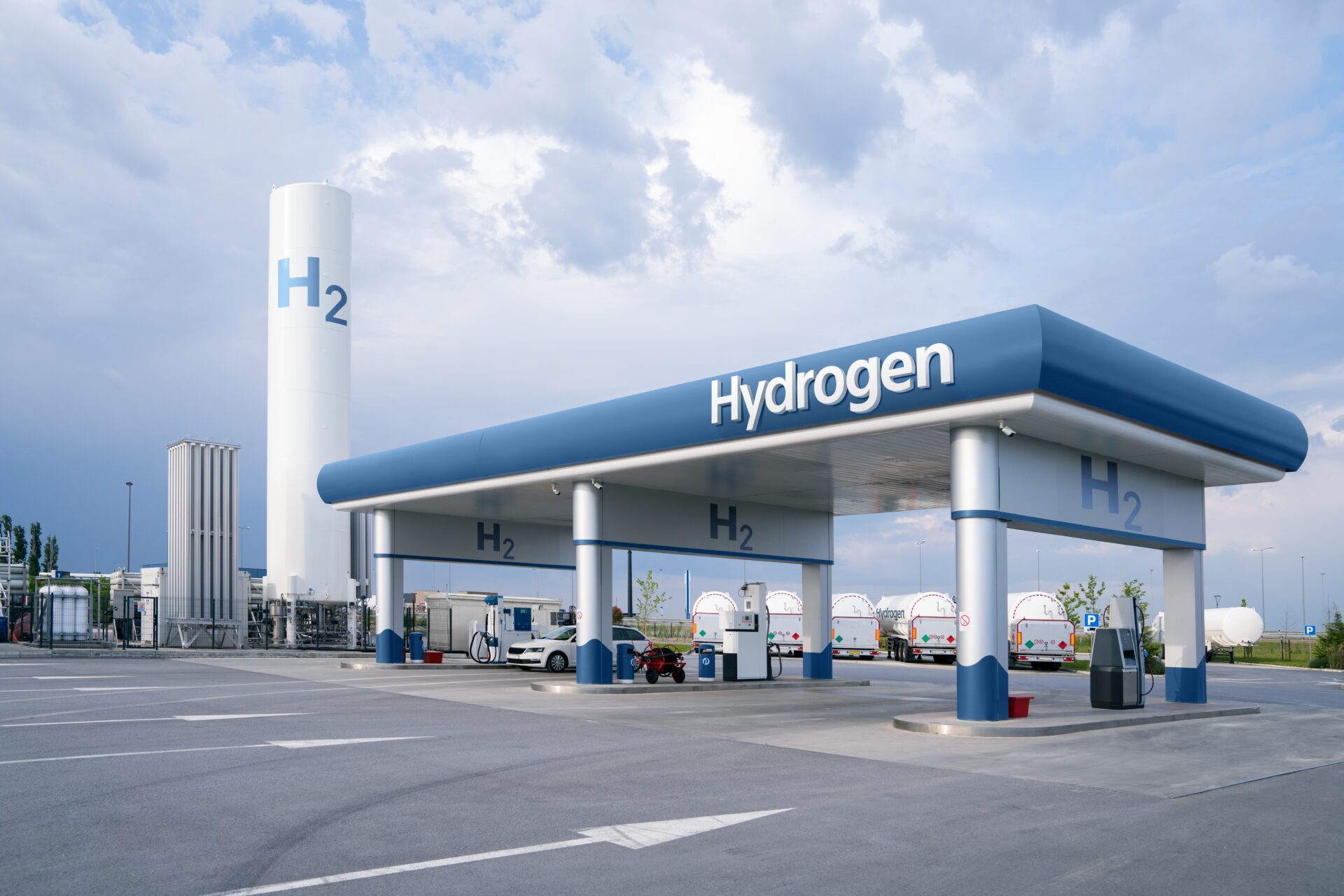
Une optimisation constante de la technologie de pile à combustible
Une pile à combustible est constituée d’un empilement de multiples cellules, chacune constituée de plaques dites " bipolaires ", qui enserrent un milieu actif où a lieu la réaction chimique. Plus on ajoute de cellules les unes derrière les autres, plus on augmente la puissance de la pile.
Historiquement, ces plaques bipolaires étaient construites en graphite, un matériau bon conducteur de courant, stable dans l’environnement chimique de la pile (donc résistant à la corrosion), mais qui obligeait de construire des plaques bipolaires très épaisses et lourdes, à la base de piles à combustible efficaces mais très volumineuses. On les utilise encore aujourd’hui dans des véhicules où la taille de la pile n’est pas un enjeu, comme par exemple le train à hydrogène Alstom Coradia en Allemagne.
Pour les transports sur route (camions, voitures), il faut des piles plus petites, plus compactes, plus légères. On a alors remplacé ces plaques de graphite par de l’acier inoxydable. Avantage : les plaques sont 10 fois plus fines. Inconvénient : l’inox n’est pas stable et pas conducteur dans l’environnement de la pile, ce qui nécessite d’utiliser un revêtement d’or (conducteur électriquement et inerte chimiquement).
Il est ainsi devenu possible de faire des piles plus compactes, utilisables sur des véhicules plus petits.
Mais à cause de l’utilisation de grandes surfaces de revêtement d’or dans la pile, le problème du prix, lui, n’était pas vraiment résolu… jusqu’à maintenant.
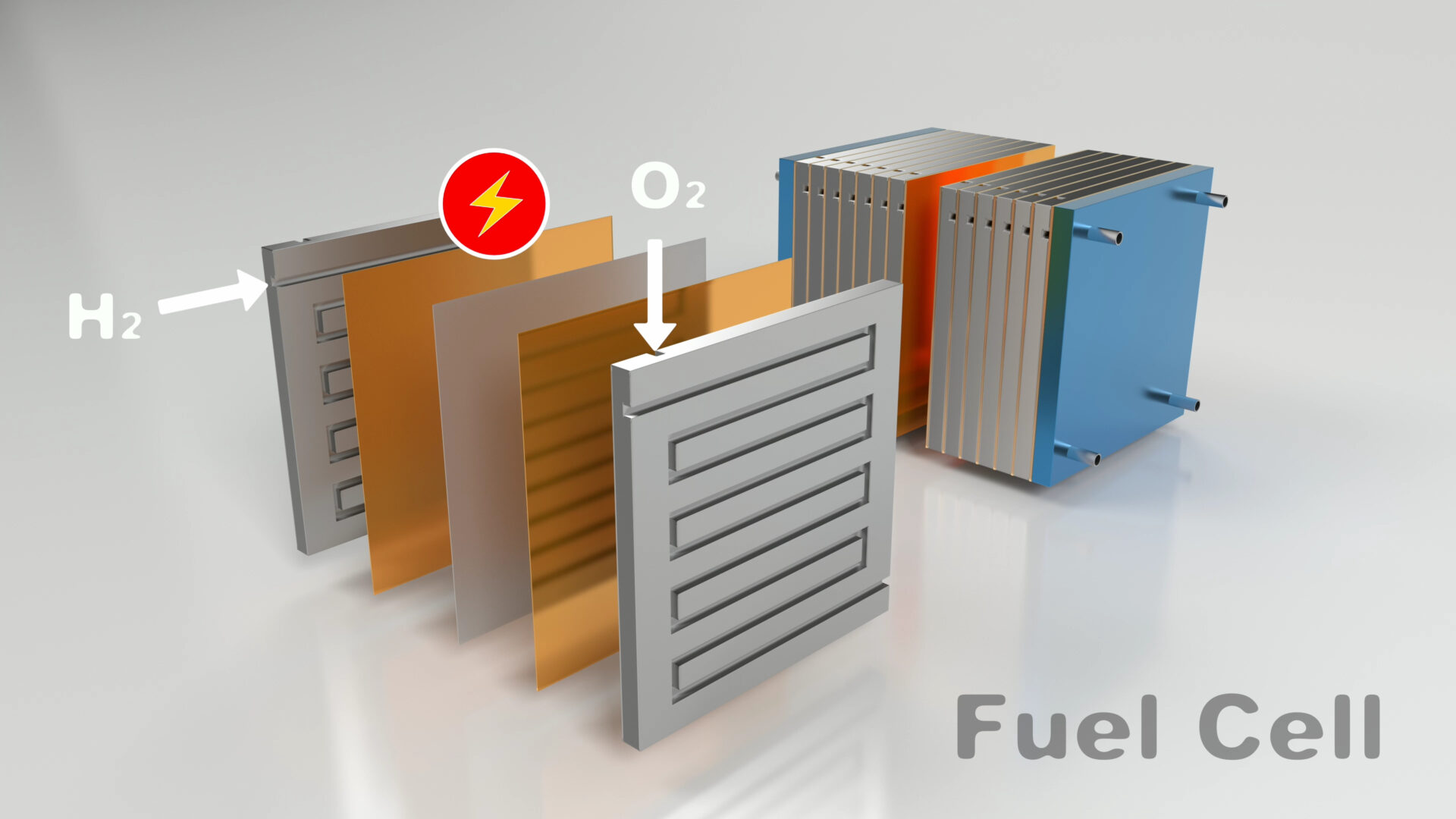
La solution technologique d’HEF
La solution d’HEF est de remplacer ce revêtement en or des plaques bipolaires par un matériau spécifique à base de carbone, pour lequel 3 brevets ont déjà été déposés. Il s’agit d’un mince film de carbone, déposé par pulvérisation sous vide, et spécialement conçu pour avoir les bonnes propriétés : entre celles du graphite (très bonne conductivité électrique) et celles du diamant (inerte chimiquement et très bonne tenue mécanique). Ce matériau n’existe pas dans la nature et doit être mis au point industriellement. Le nom de ce procédé de pulvérisation de carbone sous vide est : CERTESS (matériaux pulvérisés) ELEC (domaine électrique) FC (Fuel Cells en anglais – dédié aux piles à combustible)
L’objectif d’HEF est non seulement de développer ce matériau mais de le rendre économiquement compétitif, ce qui passe par une stratégie d’intégration verticale permettant de développer des équipements spécifiques pour que le coût de production (en plus du coût du matériau lui-même) soit aussi faible que possible.
HEF est ainsi passé, cette année, de la phase de R&D à la phase d’industrialisation avec l’acquisition, au sein des Halles Berthiez, de 12 000 m² auprès de la Ville de Saint-Etienne. D’ici 2027, cinq lignes de production devraient occuper cette usine pilote, équipée pour industrialiser ce nouveau procédé de revêtement de plaques bipolaires des piles à combustibles, avec une capacité de production visée équivalente à l’équipement annuel de 50 000 véhicules. L’objectif est aussi de diviser par 10 le coût de ce process par rapport aux techniques classiques, afin de rendre cette solution économiquement compétitive.