La technique dite du chrome dur consiste à déposer sur des pièces un fin revêtement de Chrome afin d’augmenter leur dureté, leurs propriétés de frottement, leur tenue à l’usure et à la corrosion.
Ce dépôt se fait par un procédé de traitement de surface électrochimique appelé dépôt électrolytique de chrome fonctionnel. Il consiste à utiliser des courants électriques dans un bain d’acide chromique pour déposer sur les pièces une fine couche de chrome métallique, durcissant et protectrice, dont l’épaisseur est comprise entre 5 et 150 microns.
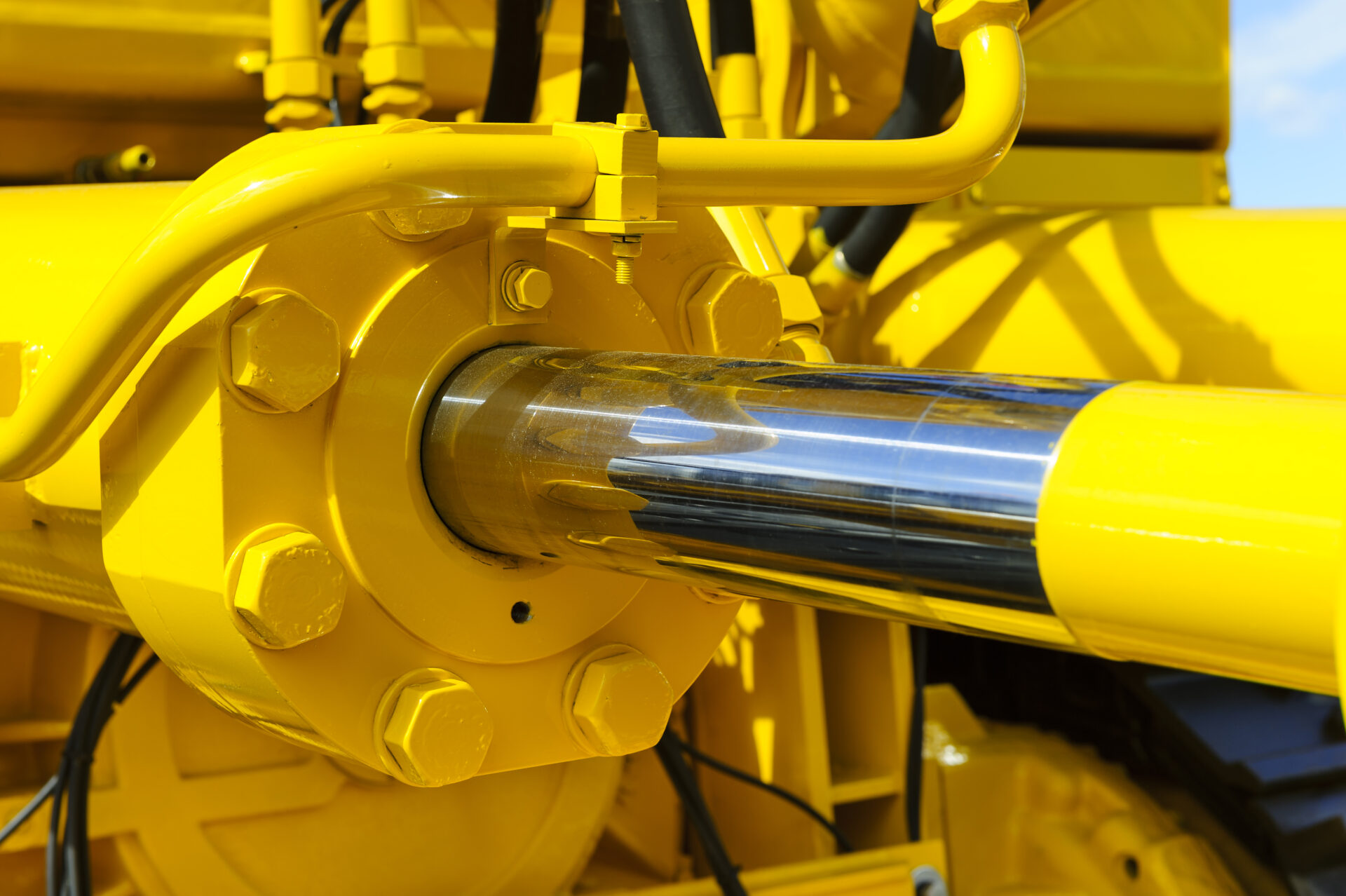
Afin de permettre le dépôt de chrome métallique, les sels de chrome à base d’acide chromique (CrO3 ou H2CrO4) sont utilisés. Ces substances chimiques sont constituées de l’élément chrome sous forme hexavalente (aussi appelé chrome VI, ou Cr6+).
Cette forme ionique du chrome possède un très fort pouvoir oxydant, et de ce fait, il est fortement toxique. Il est classé comme mutagène, cancérogène et reprotoxique, dangereux pour les opérateurs et nocif pour l’environnement.
Ce chrome hexavalent se retrouve à toutes les étapes de la production, dans les bains d’acide, mais aussi dans l’air respiré, les eaux de rinçage, les boues industrielles et en résidu sur les lignes de montage. Cette omniprésence d’un composé toxique dû à son utilisation pose de sérieux problèmes.
C’est pour cette raison que de nombreuses organisations visent à restreindre l’utilisation de chrome hexavalent, et par conséquent du procédé de chromage dur.
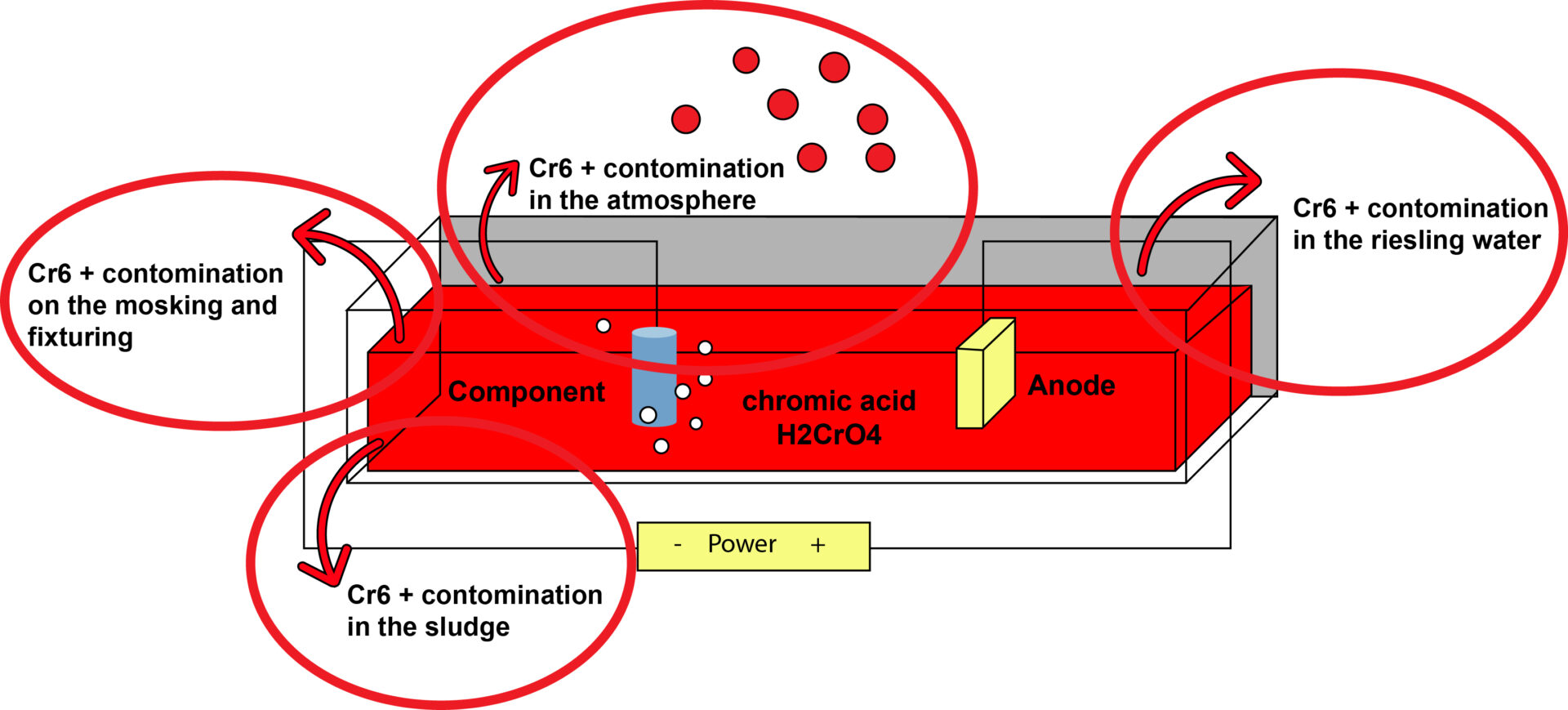
Bain de chromage dur illustrant les différentes contaminations par Chrome hexavalent.
Ce traitement durcisseur des pièces par dépôt de Chrome est depuis longtemps largement utilisé. Le grand public en connaît quelques exemples avec les pistons de vérins hydrauliques des pelleteuses (et autres engins de chantiers), les soupapes de voitures ou les tiges chromées servant de pivot dans des quantités de pièces articulées.
Pour faire face aux enjeux de santé et environnementaux contraignants le chromage dur, tout en répondant aux problématiques tribologiques de ses clients, HEF utilise des traitements de surface performants appelés traitements thermochimiques.
Les traitements de surface thermochimiques consistent à modifier la couche superficielle d’un matériau par une combinaison de réactions chimiques et d‘énergie thermique.
Ils provoquent la diffusion d’éléments atomiques (Bore, Carbone, Azote, Aluminium…) à l’intérieur de la surface traitée. Le processus modifie directement la composition chimique et la microstructure de la surface du matériau, lui conférant ainsi les propriétés recherchées.
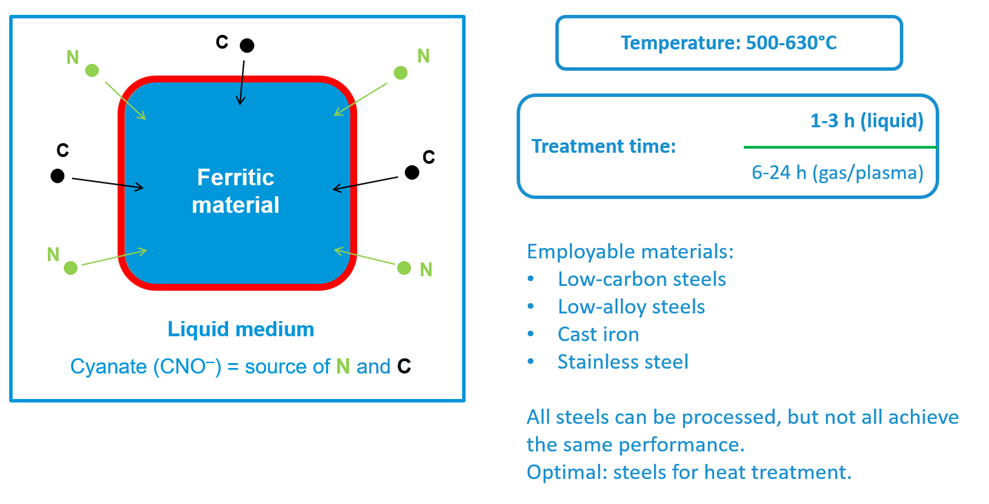
Il est à noter que contrairement au traitement de chrome dur, aucun ajout métallique n’est déposé sur les pièces. Il s’agit ici de modifier la composition chimique de la surface elle-même, afin de lui conférer les capacités de dureté et de résistance désirées.
La nitrocarburation en milieu liquide s’avère être la variante du process qui offre les plus importants avantages dans les systèmes tribologiques. Dans ce procédé, le matériau est immergé dans un bain de sels fondus à base de cyanate (CNO–), source, principalement d’Azote, mais aussi d’un peu de Carbone. Le transfert thermique élevé et la composition des sels vont alors provoquer la diffusion de ces espèces chimiques dans le matériau traité.
En extrême surface, l’Azote diffusé réagit avec le Fer pour donner une première couche (appelée couche de combinaison) de nitrure de Fer, dont l’épaisseur dépendra de la chimie du bain, du temps de traitement (de l’ordre de l’heure) et de la composition de l’acier. C’est cette couche qui va contribuer à l’augmentation de la dureté superficielle du matériau traité, mais qui va aussi jouer un rôle majeur dans les propriétés de frottement et anticorrosion des composants nitrurés.
En-dessous de cette couche de combinaison (dont l’épaisseur varie entre 1 et 30 microns) l’Azote continue à se diffuser, mais en des proportions de plus en plus faibles en fonction de la profondeur. C’est la couche de diffusion (de 50 à 500 microns), caractérisée par un gradient de dureté qui diminue progressivement pour retrouver, en profondeur, celle du métal originel.
Cette couche de diffusion est tout aussi importante, car son gradient de dureté apporte une résistance à la fatigue pour la pièce traitée.
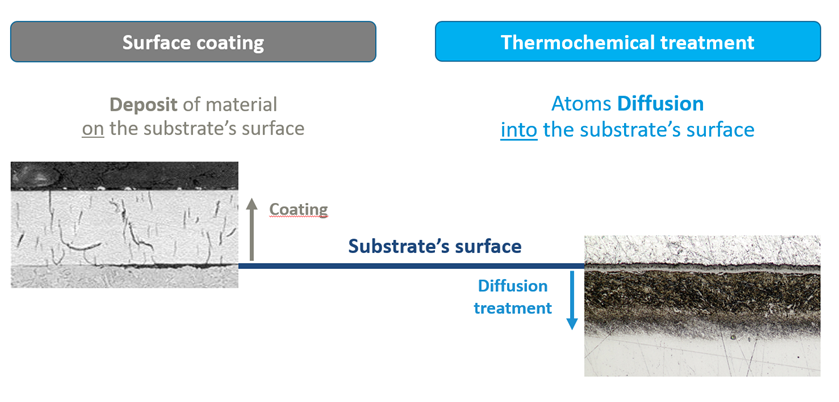
Suite à ce processus de nitruration, HEF associe dans sa ligne de traitement la possibilité d’oxyder une très mince couche de surface traitée, ce qui apportera en plus une forte résistance à la corrosion et un maintien prolongé des conditions de lubrification hydrodynamique, retardant les risques d’usure critique de pièces soumises à des efforts de frottement sous charge élevée, en cas de rupture du film lubrifiant.
Ce procédé change aussi l’aspect visuel des pièces traitées. Au lieu d’être brillante avec l’ancien revêtement de Chrome, elles seront maintenant soit grises (si elle n’ont pas été passées par une étape d’oxydation), soit noires si elles ont été oxydées (par formation d’oxyde de Fer (magnétite Fe304), très stable vis-à-vis de la corrosion).
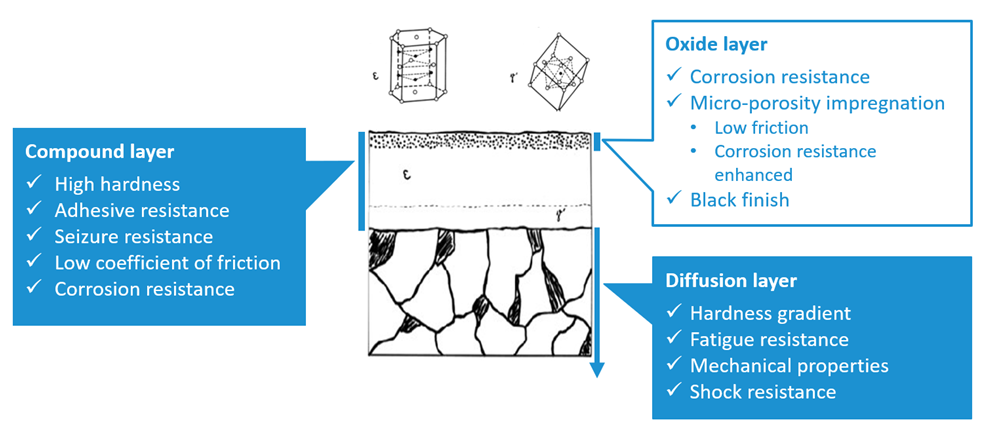
En conclusion, le traitement de nitrocarburation égale voire surpasse les avantages industriels du Chrome (meilleure résistance à l’usure et à la corrosion, propriétés de frottement supérieur avec une compétitivité économique similaire), et apporte des propriétés mécaniques supplémentaires, comme la résistance à la fatigue et une meilleure tenue en flexion (en jouant sur la profondeur de diffusion dans le matériau). De plus, et contrairement au Chrome, ce procédé n’est pas sensible à l’écaillage du revêtement (puisqu’il n’y en a pas).
Enfin, cette technique répond aussi aux préoccupations environnementales, puisqu’elle opère en milieux liquides, milieux qu’HEF est capable de recycler pour recréer ces bains de sels qu’on peut directement utiliser sur les lignes de production, ce qui induit :
- Une diminution de l’impact sur les ressources naturelles,
- Un accroissement de la compétitivité du traitement long terme. En effet, cela permet à HEF et à ses clients de réduire leur dépendance quant au risque dû à l’inflation du coût des consommables et matières premières.
- Une fabrication locale des consommables, au plus près des lignes présentes partout dans le monde, limitant ainsi l’empreinte CO2 des consommables par diminution des besoins de transports.
- La réutilisation et la revalorisation de 99 % des sous-produits : en réinjectant le sel issu du recyclage directement en production, et en valorisant les autres sous-produits crées lors de l’opération en matériaux utilisables par l’industrie (cimenterie notamment).
Les technologies CLIN™, par le biais du procédé d’innovation ECO-CLIN™, généreront donc à terme 0 déchet ultime, et deviendront de fait la technologie de Nitrocarburation avec le plus faible impact environnemental.
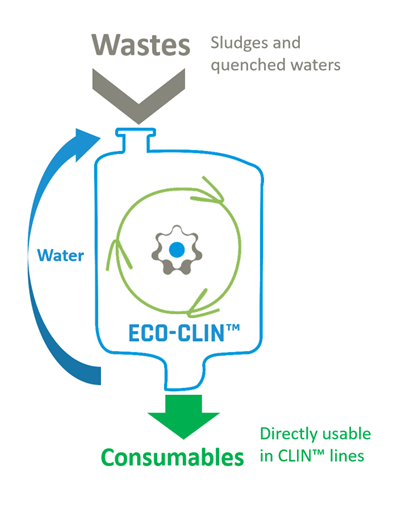