Utilisation des alliages cuivreux dans les applications Industrielles
Dans de très nombreuses applications telles que les turbines hydroélectriques, les grues, les engins de TP, ou encore l’agriculture (moissonneuses-batteuses, semoirs), ces bagues ont longtemps été fabriquées à base d’alliage cuivreux, comme le bronze (cuivre + étain), le laiton (cuivre et zinc) ou d’autres alliages à base de cuivre.
Ces alliages cuivreux sont aujourd’hui couramment (et improprement) appelés " bronzes ". Comme il s’agit de la dénomination la plus utilisée dans le langage courant, c’est ainsi que nous l’appellerons dans la suite de l’article.
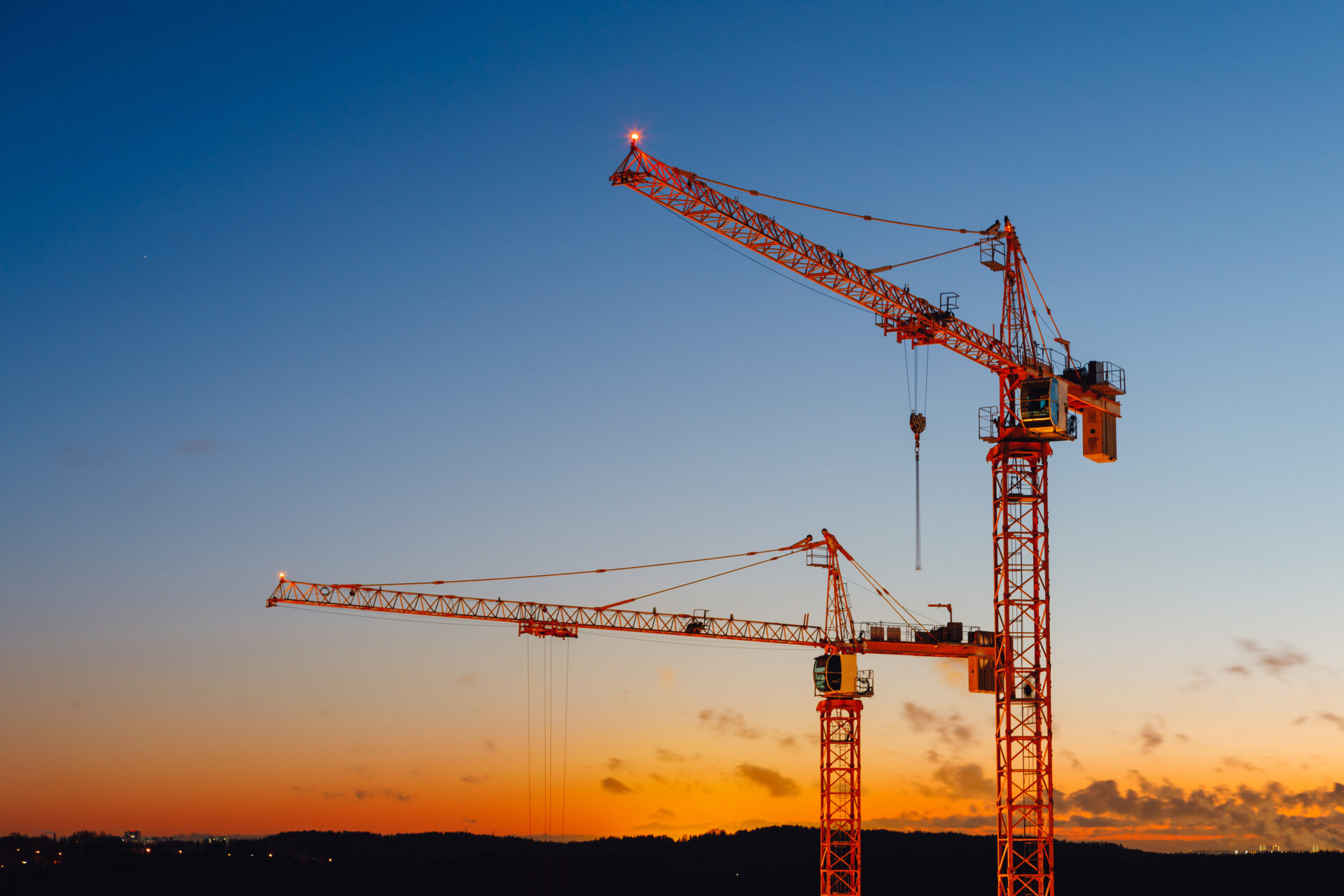
L’innovation au service de l’environnement
Les bagues ont longtemps été fabriquées à partir de bronze au Plomb. Cet alliage était utilisé pour sa très bonne résistance à la corrosion, à l’abrasion, et, dans le cas qui nous intéresse, aux frottements. Ses excellentes caractéristiques de glissement et de fonctionnement à sec lui garantissaient aussi une absence de risque de grippage, (contrairement à l’acier traditionnel). C’est donc assez naturellement qu’il a été utilisé pour la conception d’articulations.
Plus tard, l’utilisation du Plomb dans ces alliages a été progressivement éliminée, pour des raisons sanitaires (intoxications au Plomb) et environnementales. Les bagues ont alors été fabriquées à partir d’alliages cuivreux classiques, sans Plomb, mais au prix d’une légère baisse de performance des pièces, d’où le développement de nouveaux composants de frottements dits " composites " de nouvelle génération.
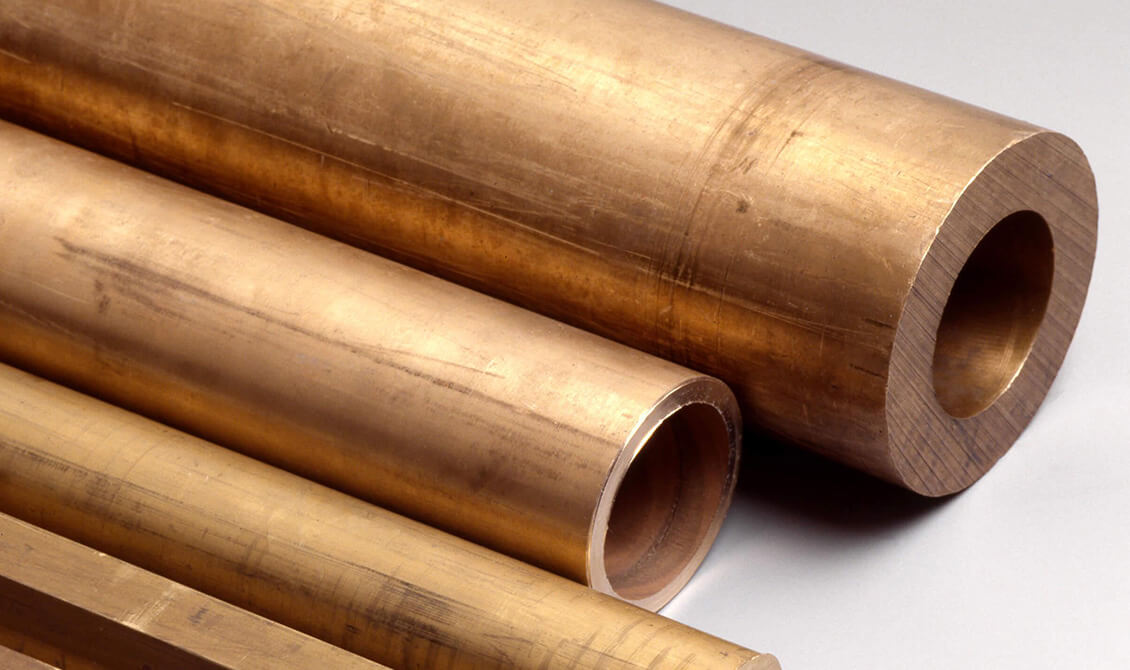
Le composite, une solution historique et pérenne
Une bague composite n’est pas composée d’alliages métalliques mais d’éléments dits " organiques ". Les matériaux composites sont formés à partir de renforts , fibre ou tissus, puis imprégnés d’un liant organique (une résine) dite thermodurcissable (c’est-à-dire que, partant d’un produit initial fluide, elle passe par une étape de polymérisation, irréversible, qui aboutit à un produit fini solide qui ne ramollit plus à la chaleur, contrairement au plastique). Ce genre de résine garde d’excellentes propriétés mécaniques même lorsque la température atteint 100 à 200°C.
Un autre avantage est celui de la lubrification. Les bagues en bronze, en aluminium ou en acier doivent être lubrifiées, avec des huiles ou plus souvent des graisses, sous peine de générer du frottement et de l’usure.
Dans le cas des bagues composites, on rajoute dans la résine (ou dans le tissu) des charges autolubrifiantes. Ce sont des microparticules de lubrifiants solides qui sont intégrées à la résine et restent contenues dans la bague une fois mise en forme. Ces ajouts permettent de baisser le coefficient de frottement pour réduire les efforts nécessaires aux mouvements des articulations et réduire l’usure, sans avoir besoin d’ajouter du lubrifiant extérieur lors de leur utilisation. Ces bagues composites sont appelées " autolubrifiantes ".
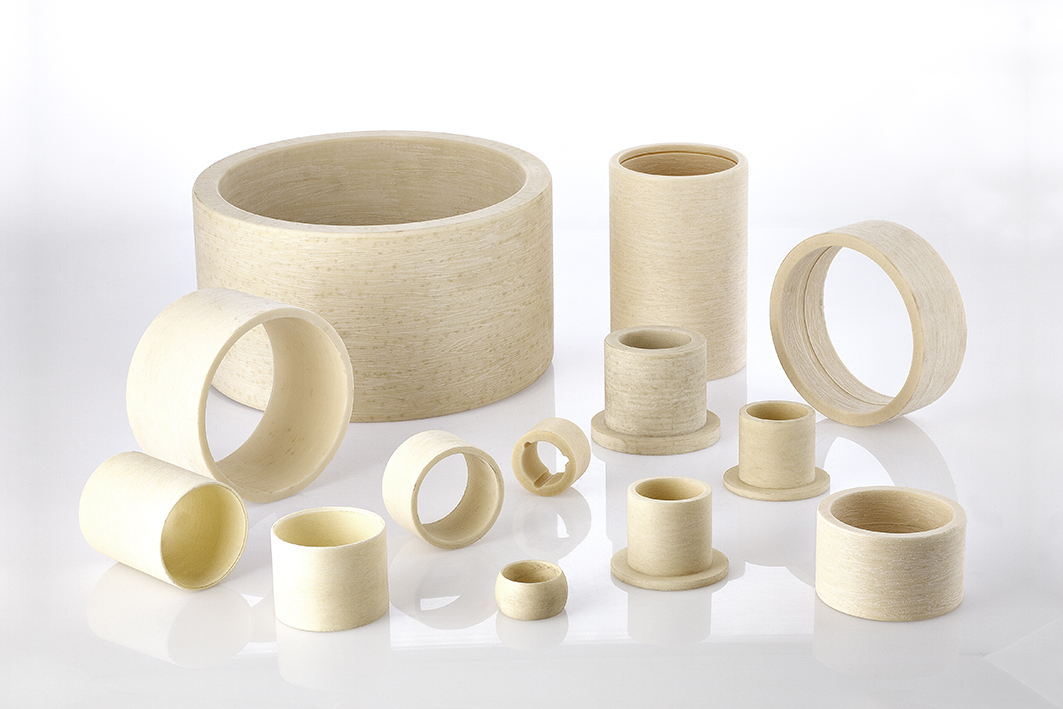
Des avantages nombreux
Le premier avantage à l’utilisation d’éléments composites est économique. Les coussinets composites autolubrifiants libèrent de la contrainte d’ajouter graisses et autres huiles pour en réduire l’usure. Cette baisse des coûts d’utilisation s’ajoute à une baisse des coûts de fabrication et d’achat.
En effet, les solutions classiques en bronze nécessitent de grandes quantités de cuivre, élément essentiel de ces alliages. Or le prix du cuivre est en constante augmentation ces dernières années. Entre 2022 et 2024, son prix a doublé. En cause : une forte demande dans le domaine de la transition énergétique, où les moteurs thermiques vont progressivement être remplacés par des moteurs électriques contenant 4 fois plus de cuivre que les moteurs thermiques. Sans compter l’industrie des énergies renouvelables, très gourmande elle aussi en cuivre (pour les éoliennes offshores, par exemple, qui nécessitent de produire de très longs câbles maritimes).
Les bagues composites autolubrifiantes ont même un coefficient de frottement plus bas encore que des bagues en alliage cuivré graissées. Ces montages nécessitent donc moins d’énergie pour bouger la bague par rapport à l’axe, c’est donc moins d’émissions de CO2.
Autre avantage des solutions HEF développées depuis maintenant plus de 20 ans, la durée de vie des pièces est augmentée par rapport aux solutions en bronze. Cette augmentation est quantifiée et certifiée par des essais sur banc, mais aussi validée par les retours de nos clients.
L’utilisation de matériaux composites permet une substantielle réduction de poids par rapport aux composants métalliques (leur densité est 5.5 fois plus faible que des solutions en alliage cuivreux). A titre d’exemple, une bague de grosse dimension (200 mm de diamètre intérieur, 250 mm extérieur et 200 mm de longueur) en alliage cuivreux pèse 31 kg. Ce poids est réduit à 5.5 kg pour les composites, ce qui permet aussi une manutention plus facile, plus rapide et moins coûteuse.
Enfin, les solutions HEF avec renfort de fibre de verre ou non permettent de tenir des charges très élevées (jusqu’à 140 MPa, contre 60 MPa pour les pièces en alliage cuivreux).
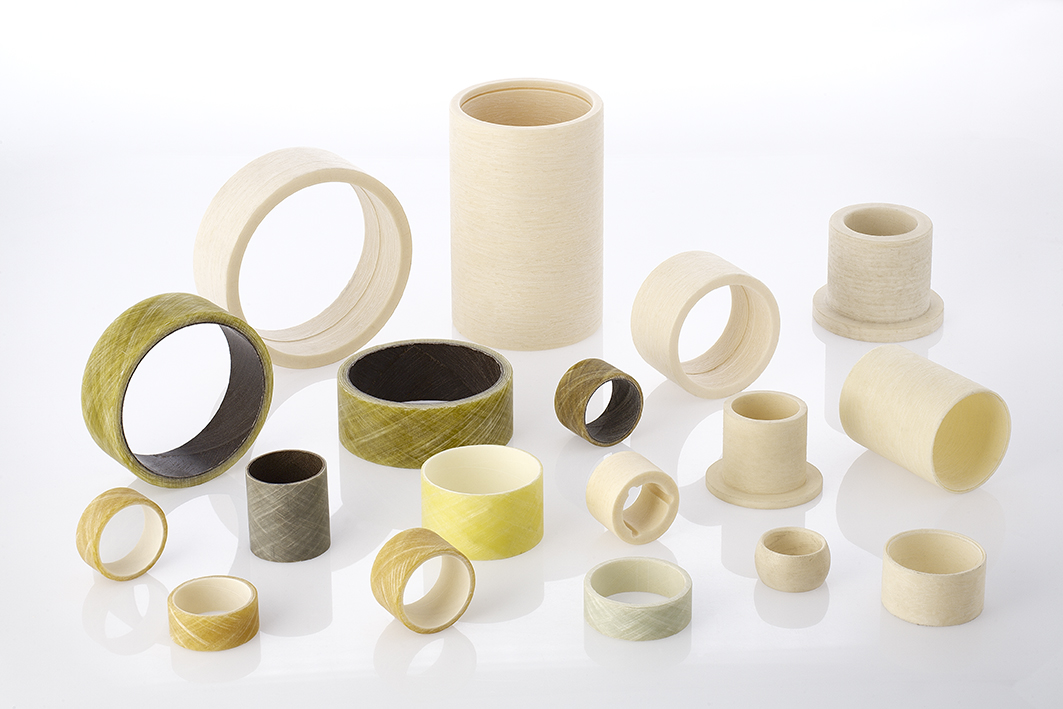
Et la pièce antagoniste ?
Le fait de supprimer la lubrification nécessite de protéger la pièce antagoniste contre la corrosion (l’axe dans le cas d’une articulation arbre-coussinet).
Les solutions du groupe HEF, traitements (ARCORTM…) ou composants (axe PELTM OX) sont particulièrement adaptées pour les pièces frottant en face de solutions autolubrifiantes. Elles permettent d’augmenter la durée de vie des machines et des équipements.
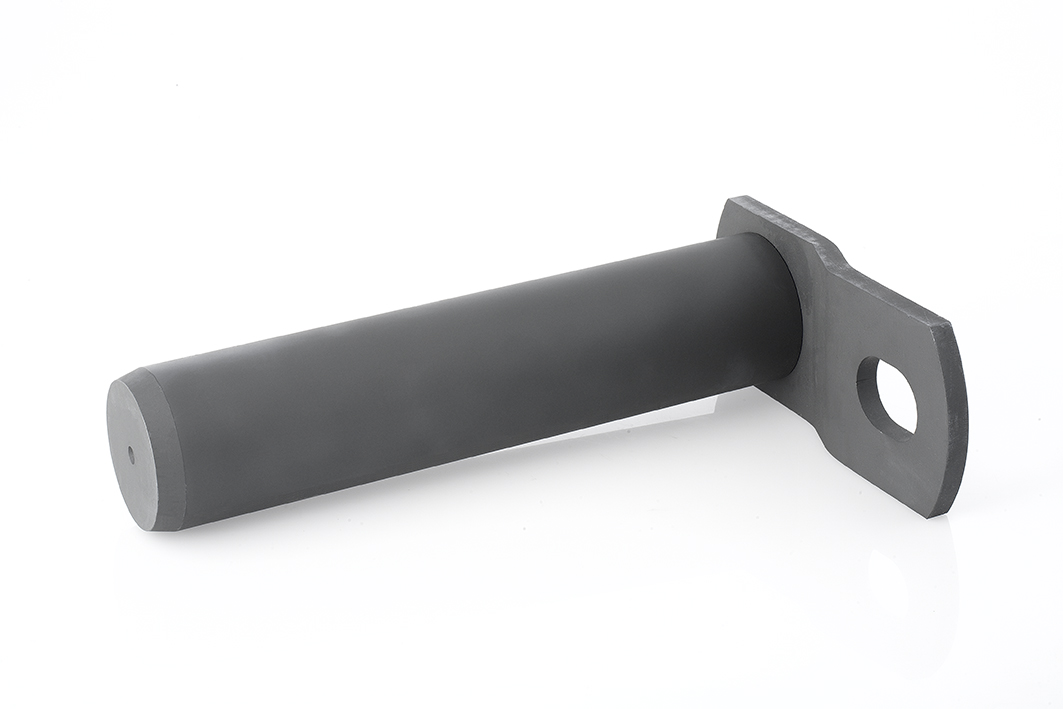
Pour qui ?
Ces bagues composites autolubrifiantes sont utilisées dans de nombreux domaines et sur de nombreuses machines. On les retrouve dans l’industrie hydroélectrique (barrages, turbines), dans le domaine maritime (paliers de guidage d’hélice de bateaux, de gouvernail) ou agricole (semoirs, outils de travail du sol), pour la manutention de charges lourdes (nacelles élévatrices, grues montées sur camion) et sur les essieux de gros engins (trains, remorques de poids lourds, moissonneuses batteuses, qui bénéficient de la bonne résistance à la charge des bagues composites couplée à l’absence de besoin de lubrification externe). Grâce à leurs avantages, il y a encore de nombreux domaines où ces technologies peuvent être appliquées.
Parlez-en à nos experts; ils vous conseilleront sur la meilleure solution et vous guideront lors du design (montage, définition des jeux, rugosité…).
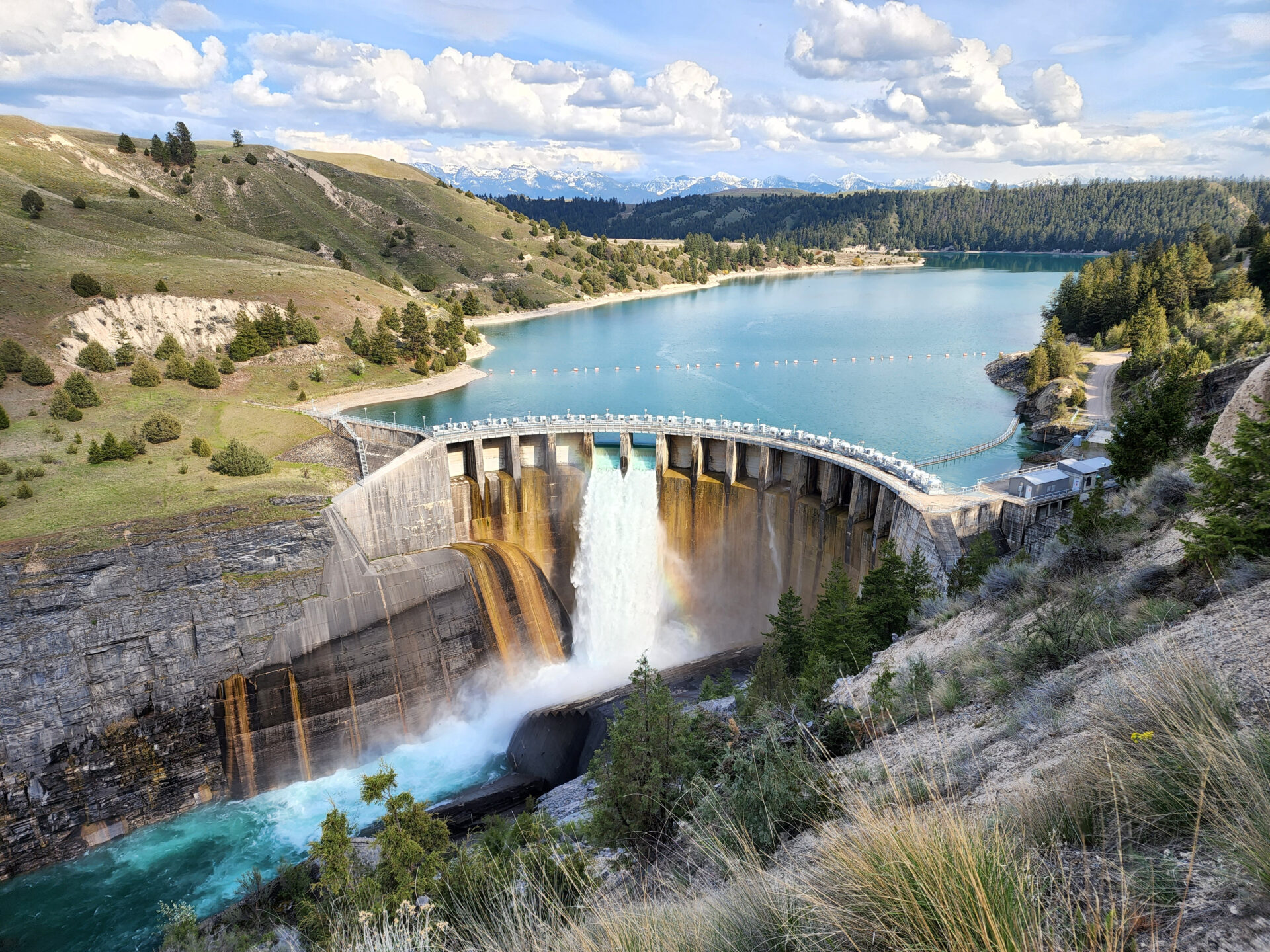
" Nous continuons à travailler chaque jour pour améliorer nos produits. Nos équipes R&D développent nos futurs produits dans l’objectif d’augmenter leurs durées, leurs performances et de mieux préserver l’environnement tout en restant dans des coûts compétitifs. " – Pierrick Pavallier, product manager friction components
Retrouvez nos gammes de bagues composites : H-LINER (S avec renfort fibre de verre, M avec des propriétés auto-lubrifiantes sur toute l’épaisseur du composant) ainsi que d’autres solutions (Tribotex et Triboglide, L2 MARINE) fabriquées par notre filiale ACM composite bearings en Grande-Bretagne.
