Use of copper alloys in industrial applications
In a wide range of applications, such as hydropower turbines, cranes, construction and agricultural machineries (combines, seeders), these bushings have long been made from copper alloys such as bronze (copper + tin), brass (copper and zinc) or other copper-based alloys
Today, these copper alloys are commonly (and improperly) referred to as “bronzes”. As this is the term most commonly used in everyday language, we’ll refer to it as such in the remainder of this article.
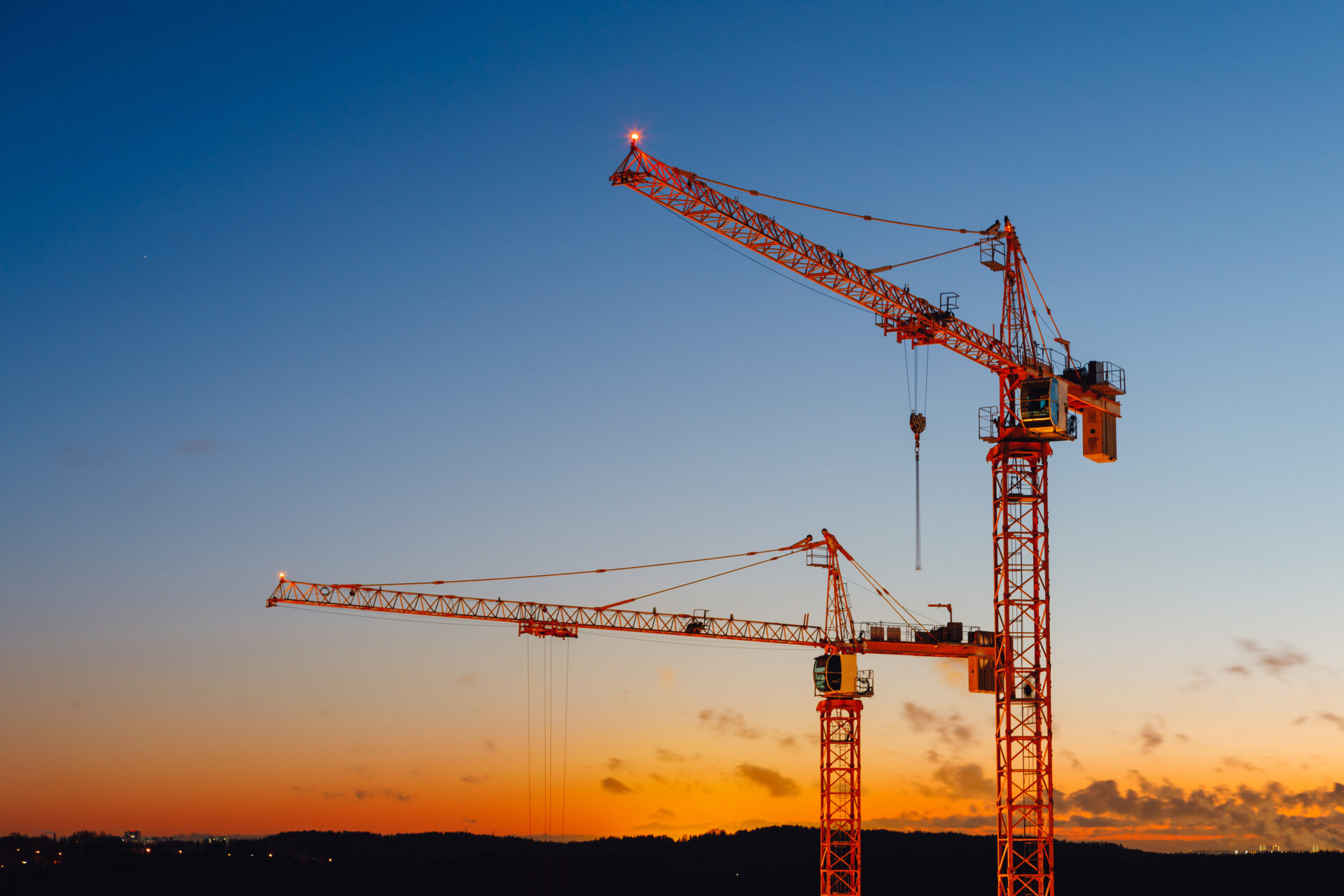
Innovation for the environment
Bushes have long been made from leaded bronze. This alloy was used for its excellent resistance to corrosion, abrasion and, in our case, its friction properties. Its excellent sliding and dry-running characteristics also ensured no risk of seizing (unlike traditional steel). It was therefore quite natural that it should be used for joint design.
Later, the use of lead in these alloys was gradually phased out, for health (lead poisoning) and environmental reasons. Bushings were then made from conventional, lead-free copper alloys, but at the cost of a slight drop in part performance, hence the development of new-generation “composite” friction components.
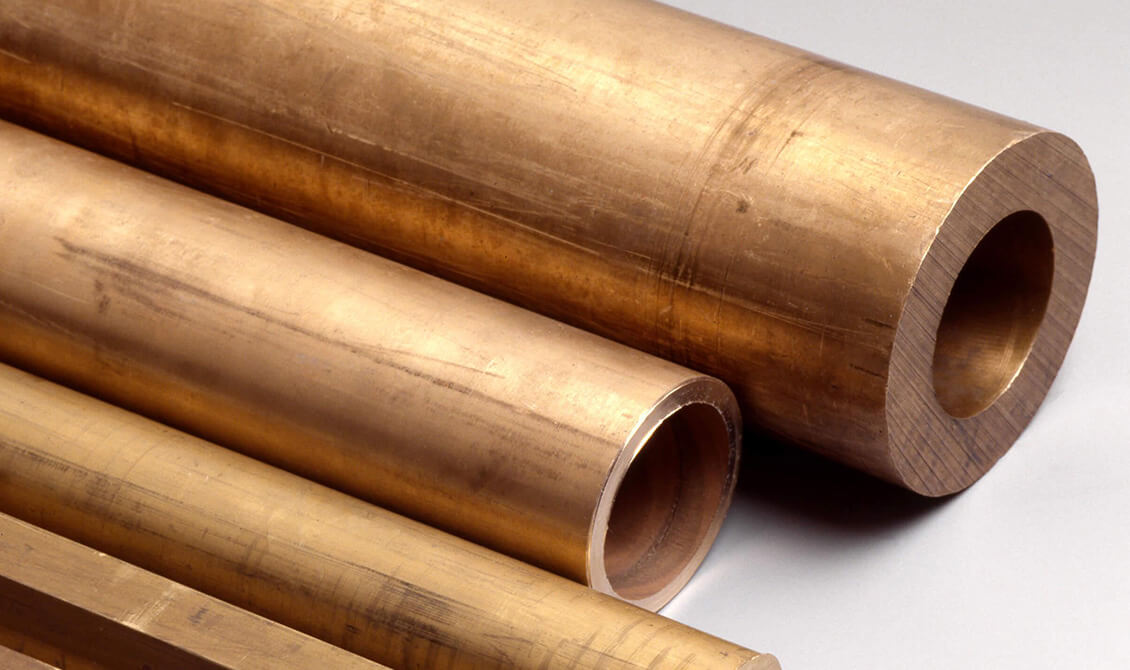
Composite, an historic and long-lasting solution
A composite bushing is not made of metal alloys, but of “organic” elements. Composite materials are formed from reinforcements, fibers or fabrics, then impregnated with an organic binder (a resin) known as thermosets (i.e., starting from a fluid initial product, it passes through an irreversible polymerization stage, resulting in a solid finished product that no longer softens under heat, unlike plastic). This type of resin retains excellent mechanical properties even at temperatures of 100 to 200°C.
Another advantage is lubrication. Bronze, aluminum or steel bushes need to be lubricated with oils or, more often, greases, otherwise they generate friction and wear.
In the case of composite plain bearings, self-lubricating fillers are added to the resin (or fabric). These are micro-particles of solid lubricant which are incorporated into the resin and remain in the bushing once it has been shaped. These additions lower the coefficient of friction to reduce the effort required for joint movement and reduce wear, without the need to add external lubricant during use. These composite bushings are called “self-lubricating”.
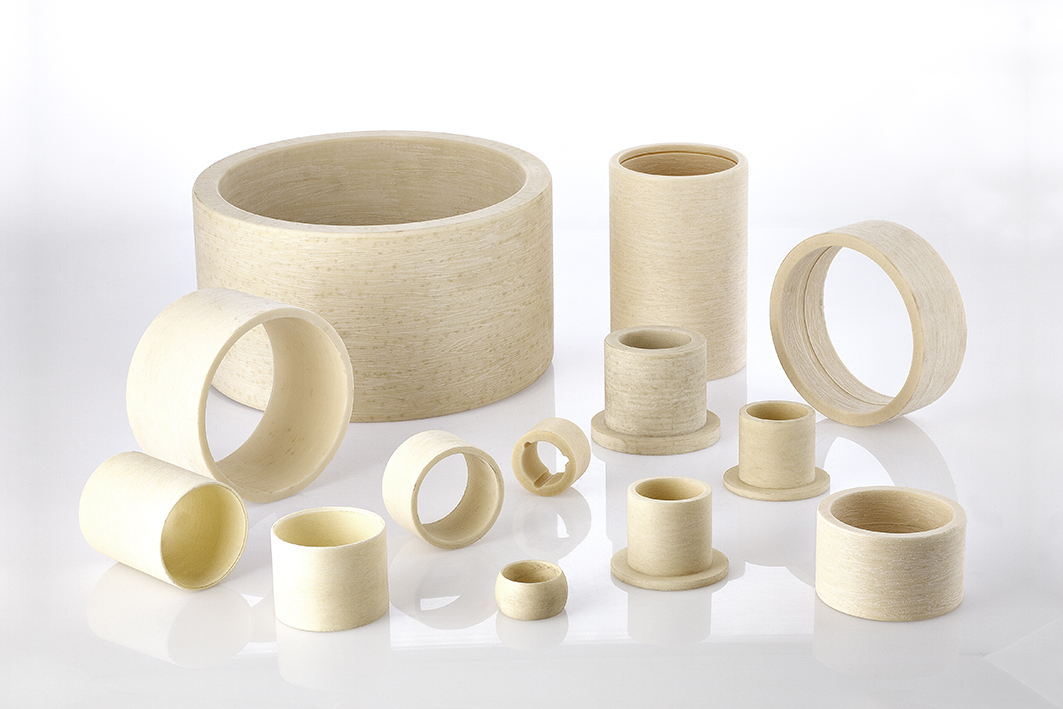
Numerous advantages
The first advantage of using composite elements is economic. Self-lubricating composite plain bearings eliminate the need to add grease and other oils to reduce wear. This reduction in operating costs comes on top of lower manufacturing and purchasing costs.
Indeed, conventional bronze solutions require large quantities of copper, an essential element in these alloys. Yet the price of copper has been rising steadily in recent years. Between 2022 and 2024, its price has doubled. The reason: strong demand in the energy transition sector, where internal combustion engines will gradually be replaced by electric motors containing 4 times more copper than internal combustion engines. Not to mention the renewable energies industry, which is also very copper-intensive (for offshore wind turbines, for example, which require the production of very long maritime cables to bring the electricity to the grid)
Self-lubricating composite bushings have an even lower coefficient of friction than greased copper alloy plain bearings. As a result, these assemblies require less energy to move the bushing around the shaft, resulting in lower CO2 emissions.
Another advantage of HEF solutions, developed over more than 20 years, is the increased service life of parts compared to bronze solutions. This increase is quantified and certified by bench tests, but also validated on the field by our numerous customers.
The use of composite materials enables a substantial weight reduction compared with metal components (their density is 5.5 times lower than copper alloy solutions). For example, a large plain bearing (200 mm inner diameter, 250 mm outer diameter and 200 mm length) made of copper alloy weighs 31 kg. This weight is reduced to 5.5 kg for composites, which also makes handling easier, faster and less costly.
Finally, HEF solutions, with or without fiberglass reinforcement, can withstand very high loads (up to 140 MPa, compared with 60 MPa for copper alloy parts). This allows for downsizing the joints and thus decreasing the cost even further.
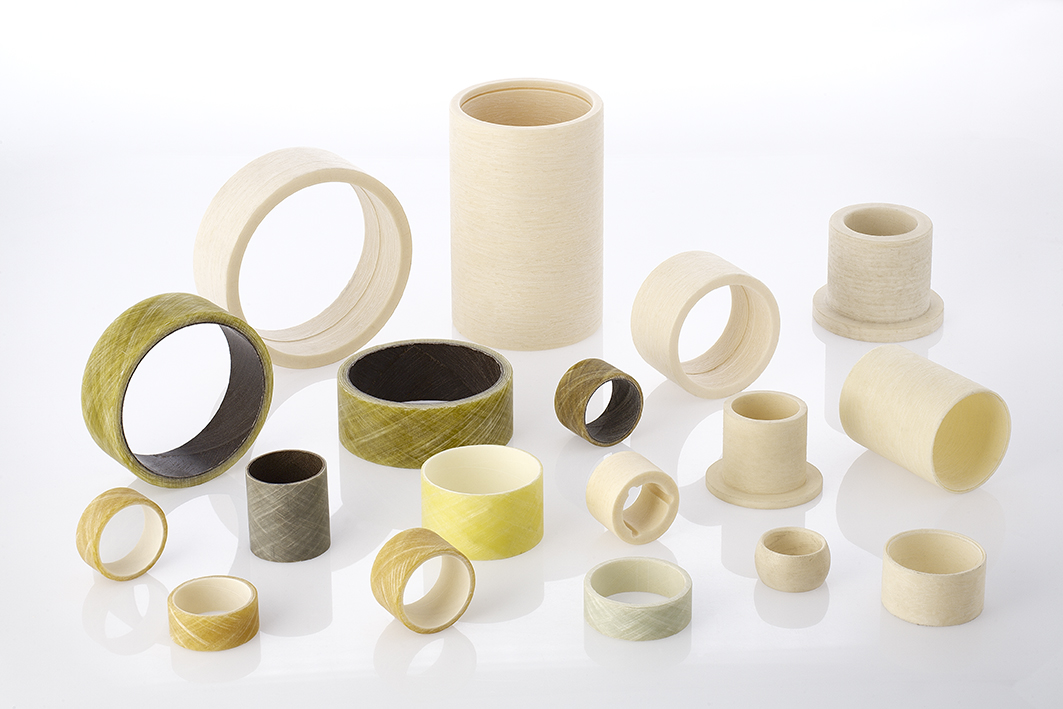
And the antagonist?
Eliminating lubrication means protecting the counterpart from corrosion (the shaft in the case of a shaft-bearing joint).
HEF Group solutions, whether treatments (ARCORTM…) or components (PELTM OX axis), are particularly suitable for parts rubbing against self-lubricating solutions. They extend the service life of machines and equipment.
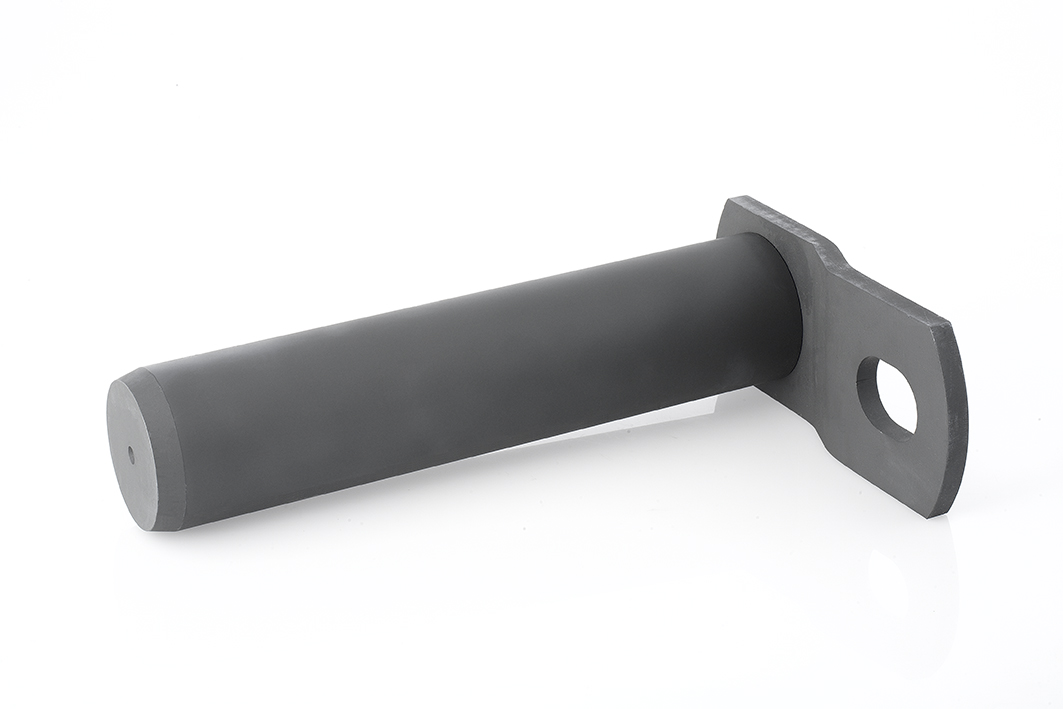
For whom?
These self-lubricating composite bushings are used in many fields and on many machines. They can be found in the hydropower plants (dams, turbines), in the marine sector (boat propeller shaft bearings, rudder bearings) or in agriculture (seeders, tillage equipment), for heavy-duty handling (aerial work platforms, truck-mounted cranes) and on the axles of large machines (trains, truck trailers, combine harvesters, which benefit from the good load resistance of composite bushings coupled with the absence of the need for external lubrication). Thanks to their advantages, there are still many areas where these technologies can be applied. Talk to our experts; they’ll advise you on the best solution and guide you through the design process (assembly, definition of clearances, roughness, etc.).
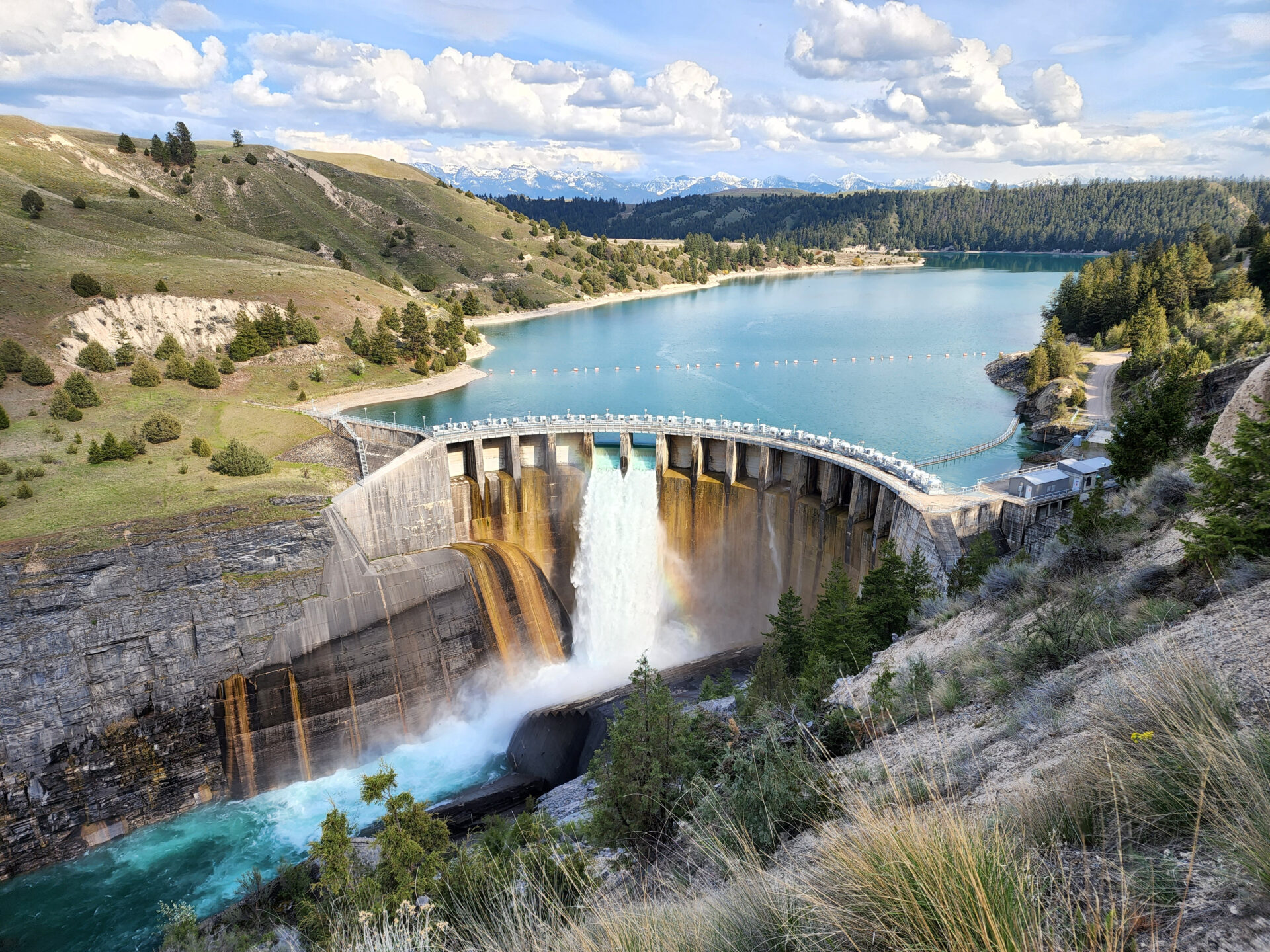
“We continue to work every day to improve our products. Our R&D teams are developing our future products with the aim of increasing their life and performance, and better protecting the environment while remaining cost-competitive. “Pierrick Pavallier, product manager friction components
Discover our range of composite bushings: H-LINER (S with fiberglass reinforcement, M with self-lubricating properties throughout the entire thickness of the component) and other solutions (Tribotex, Triboglide, ACM L2 marine) manufactured by our UK subsidiary ACM composite bearings.
