Nitrocarburizing and liquid nitriding: Tribological performance for demanding industries
With more than 60 years of experience developing thermochemical treatments, HEF is now the world leader in the field of liquid ionic nitriding. These technologies have been and are continuously improved to meet the technical, economic, and environmental requirements of industrial sectors such as mobility, construction, defense, and decarbonized energy. Thanks to its international network, HEF makes its technologies and their remarkable capabilities available worldwide.
Contact our experts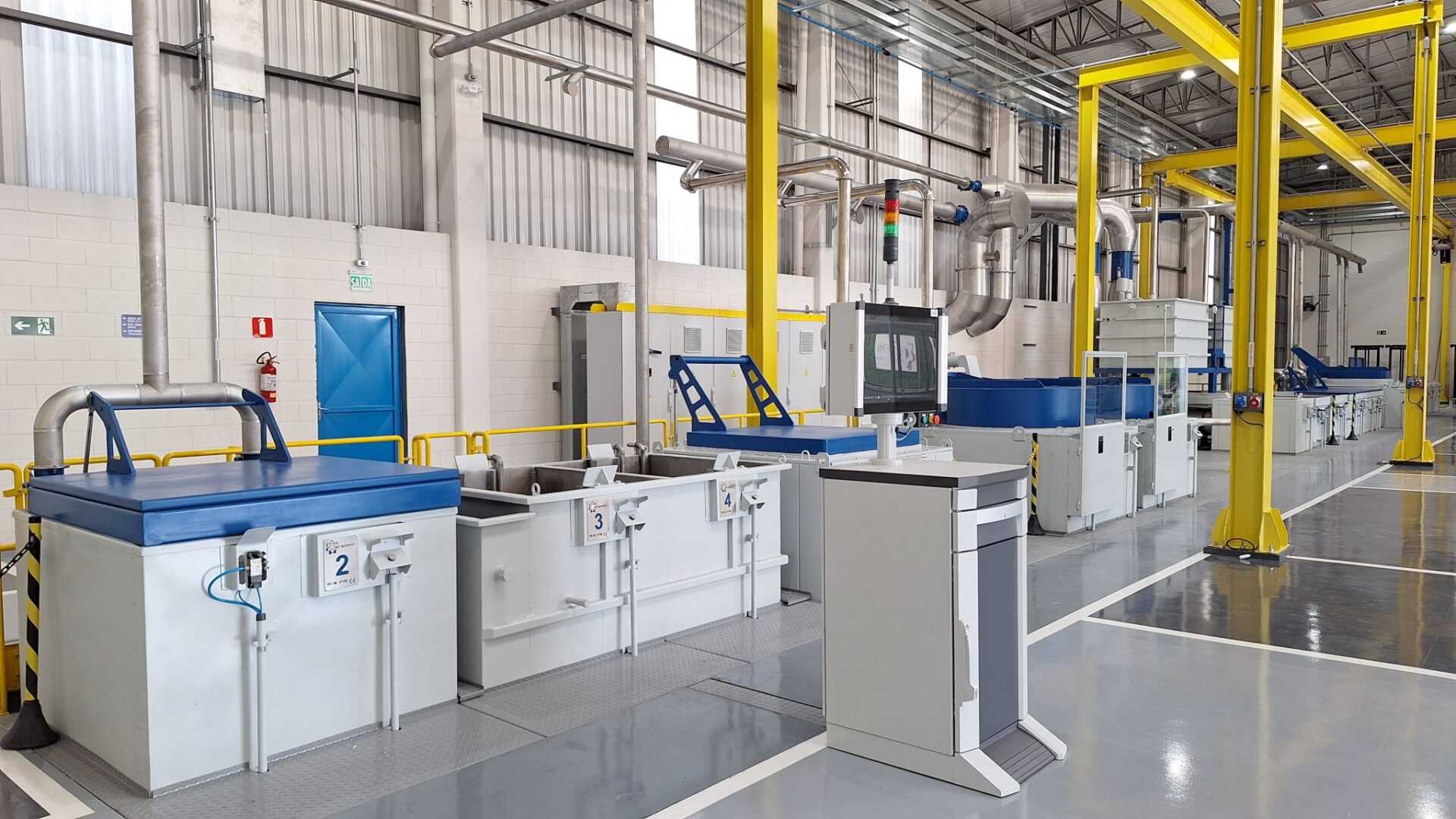
Our treatment range
The HEF group’s nitrocarburizing treatments are patented and marketed under the names ARCORTM, SURSULFTM, TENIFERTM, TUFFTRIDETM, MELONITETM, NUTRIDETM, and QPQTM.
These brands are grouped together under the name CLINTM.
These treatments are supplied by HEF through its international TECHNIQUES SURFACESTM network or they are integrated at the customer’s site, depending on the project.
Moreover, CLINTM processes emit no VOCs (volatile organic compounds) or NOx (nitrogen oxide); they use no PFAS substances (eternal pollutants) and they are REACH-compliant.
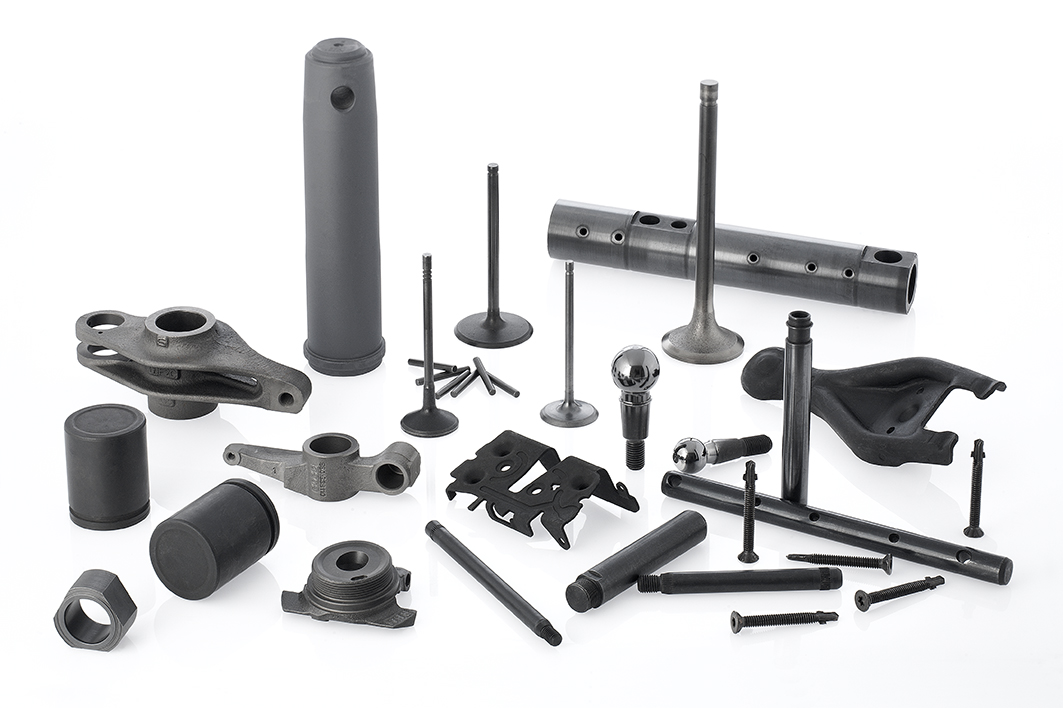
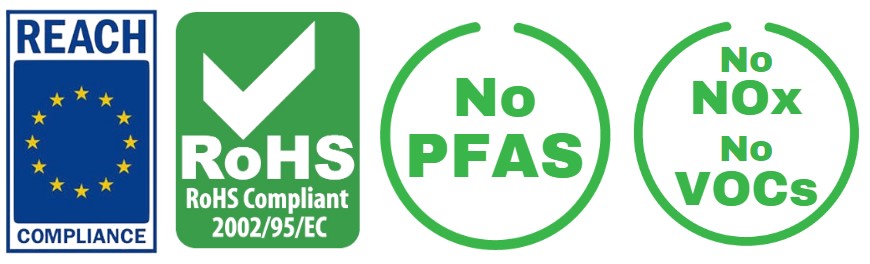
Advantages of CLIN™ technologies
CLIN™ technologies are proven alternatives to many surface treatments.
HEF positions its CLIN™ technologies as the ideal alternatives to harmful processes, such as hard-chrome plating, electroless nickel, or gas nitriding.
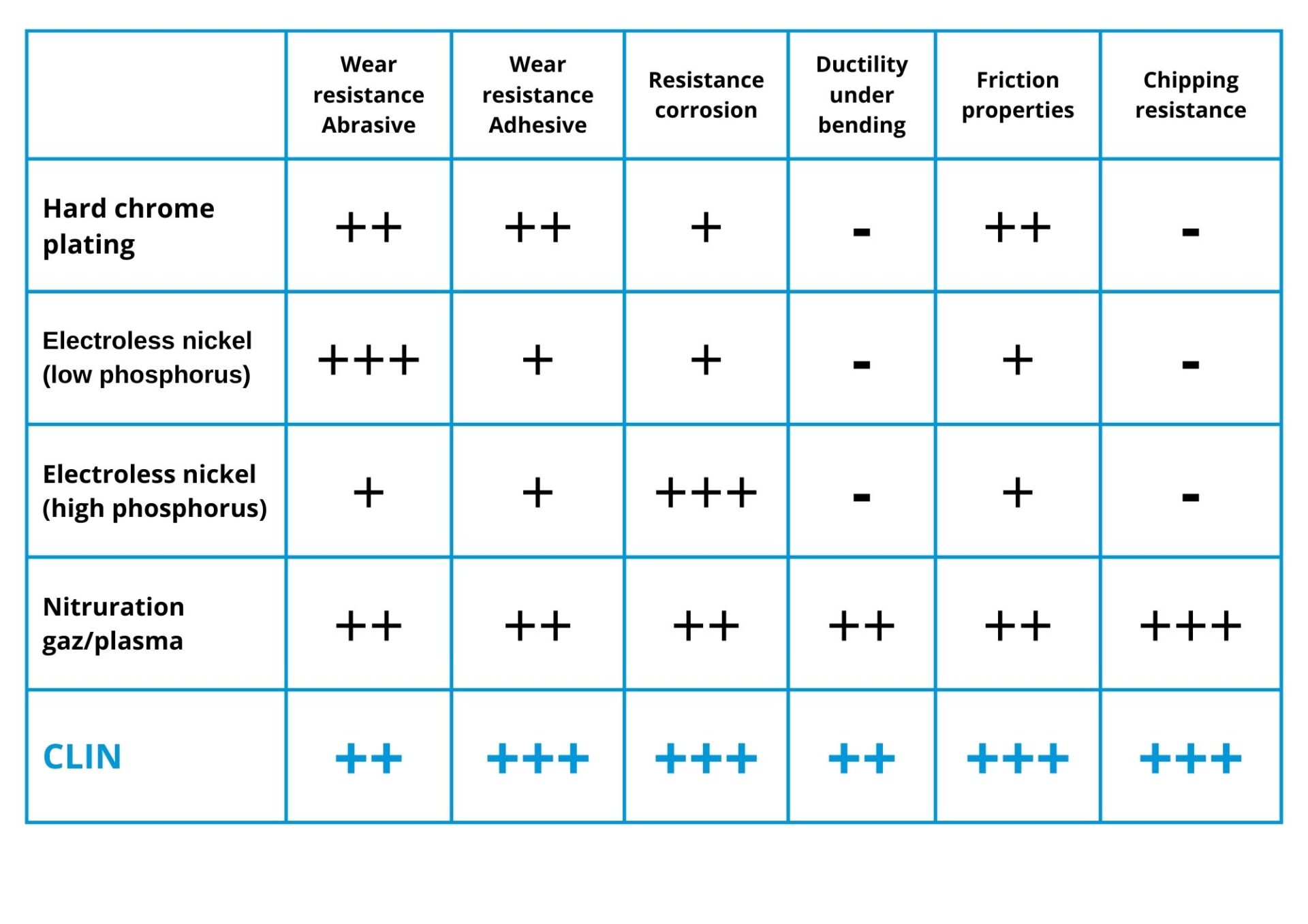
A closer look at our CLIN™ process
Liquid nitriding processes can be used to treat all types of ferrous materials, from cast irons to high-alloy steels.
CLIN™ technologies consist of a combination of steps. Among these steps, liquid nitriding is the main component.
This combination enables multiple characteristics that make processes such as ARCORTM complete and versatile treatments.
CLIN™ treatments provide major improvements with regard to:
- friction
- protection against corrosion
- fatigue strength
- resistance to abrasive wear
- resistance to adhesive wear (seizure)
Various CLIN™ product ranges are developed in response to the tribological constraints and problems faced by manufacturers. The parameters of CLIN™ processes can be adjusted to attain the desired performance.
Depending on the nitrocarburizing treatment range and the composition of the steel, the properties obtained can reach:
- up to 1200 HV in surface hardness
- up to 1000 h of corrosion resistance in the salt spray test (ISO 9227)
Application examples:
- Hinge pins
- Gas cylinders
- Hydraulic cylinders
- Differential systems
- Brake components
Controlled vertical integration
With our vertical integration approach and to assure the quality of our nitriding treatments, HEF has acquired expertise in the following areas:
- Research & development for continuous improvement of our technologies;
- Design, manufacture, optimization, and maintenance of our industrial equipment;
- The chemistry of salts and other consumables;
- Preparation and adjustment of surface states through mechanical finishing; and
- Waste management through recycling to achieve zero ultimate waste.
By building on its vertical integration strategy, HEF continues to innovate, in particular by developing and patenting our ECO-CLIN™ recycling process.
This integration model enables HEF to operate in accordance with different business models by adapting to the needs of the customer. This extends from service provision within our Techniques Surfaces entities to technology transfer, where HEF offers equipment and consumables.
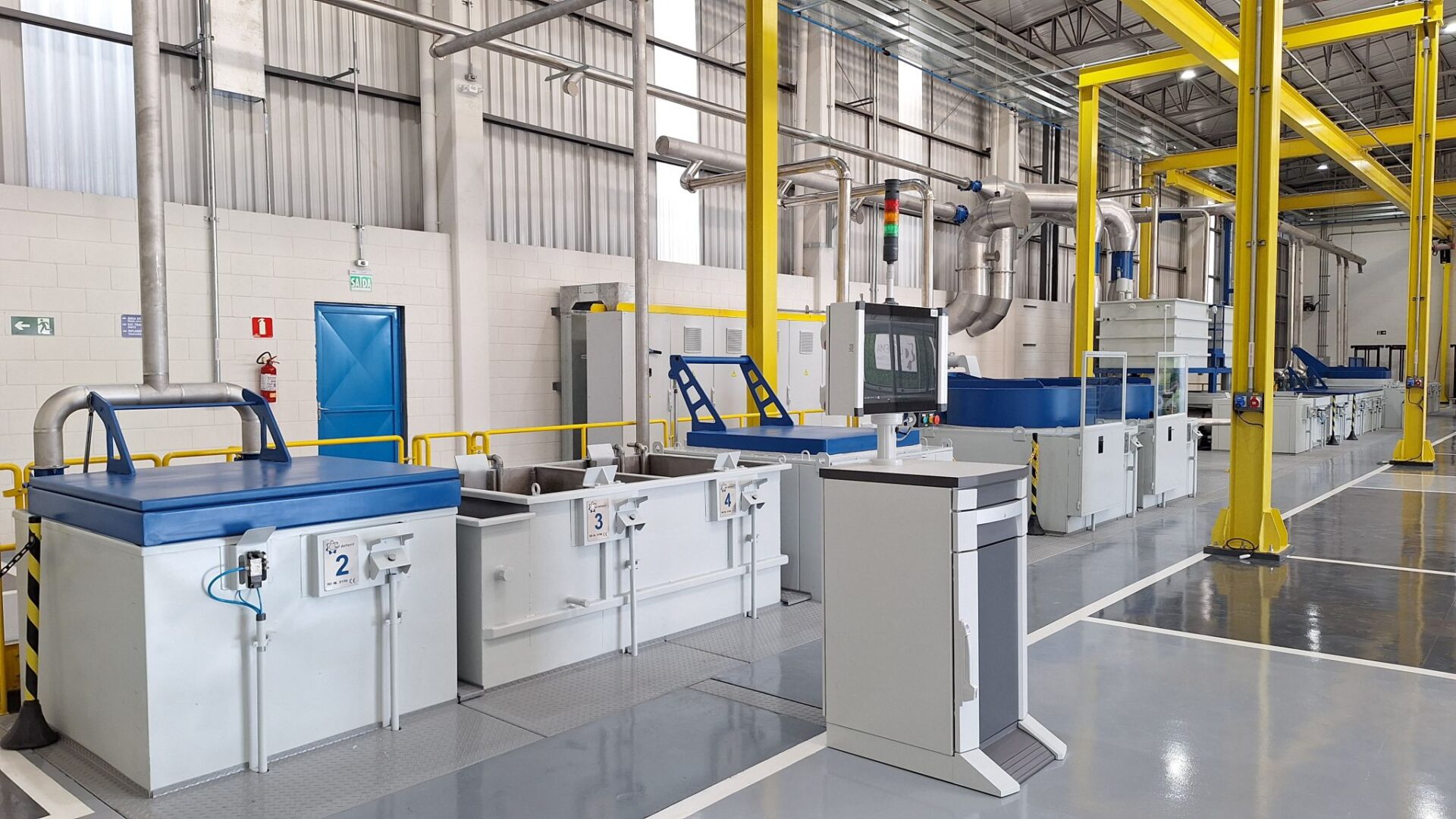
ECO-CLIN™ – A recycling process that enables the circular economy of CLIN™ technologies
Established within our Green Centers, our upcycling sites on different continents, ECO-CLIN™ limits the impact of nitrocarburizing technologies on natural resources while securing the supply of raw materials to our Green Centers.
Recycling waste into consumables that can be used directly on the CLIN™ processing lines means:
- reduced impact on natural resources;
- increased competitiveness for long-term processing that enables HEF as well as its customers to reduce risk dependence regarding the costs of consumables and raw materials due to inflation; and
- local manufacturing of consumables, as close as possible to production lines throughout the world. This, in turn, limits the CO₂ footprint of consumables by reducing the need to transport them.
The upcycling of waste generated by the CLIN™ technologies into new consumables with a 99% upcycling rate promotes a circular economy model and, at the same time, offers industries a sustainable and more responsible technology.
Conclusion
CLIN™ technologies perfectly meet the dual requirements of providing resistance for diverse parts in harsh environments while providing a sustainable solution that is capable of meeting the many needs of the market.
Thus, HEF CLIN™ technologies fall under:
- the Industry 4.0 era through the development of state-of-the-art facilities; and
- a circular economy model through the development of ECO-CLIN™ processes.