Ultra-fast femtosecond laser treatment – a high-performance technological opportunity
Ultra-fast laser processing (femtosecond laser) enables rapid functionalization, texturing, or micromachining without material deterioration, available in i2D and 3D on a wide range of materials.
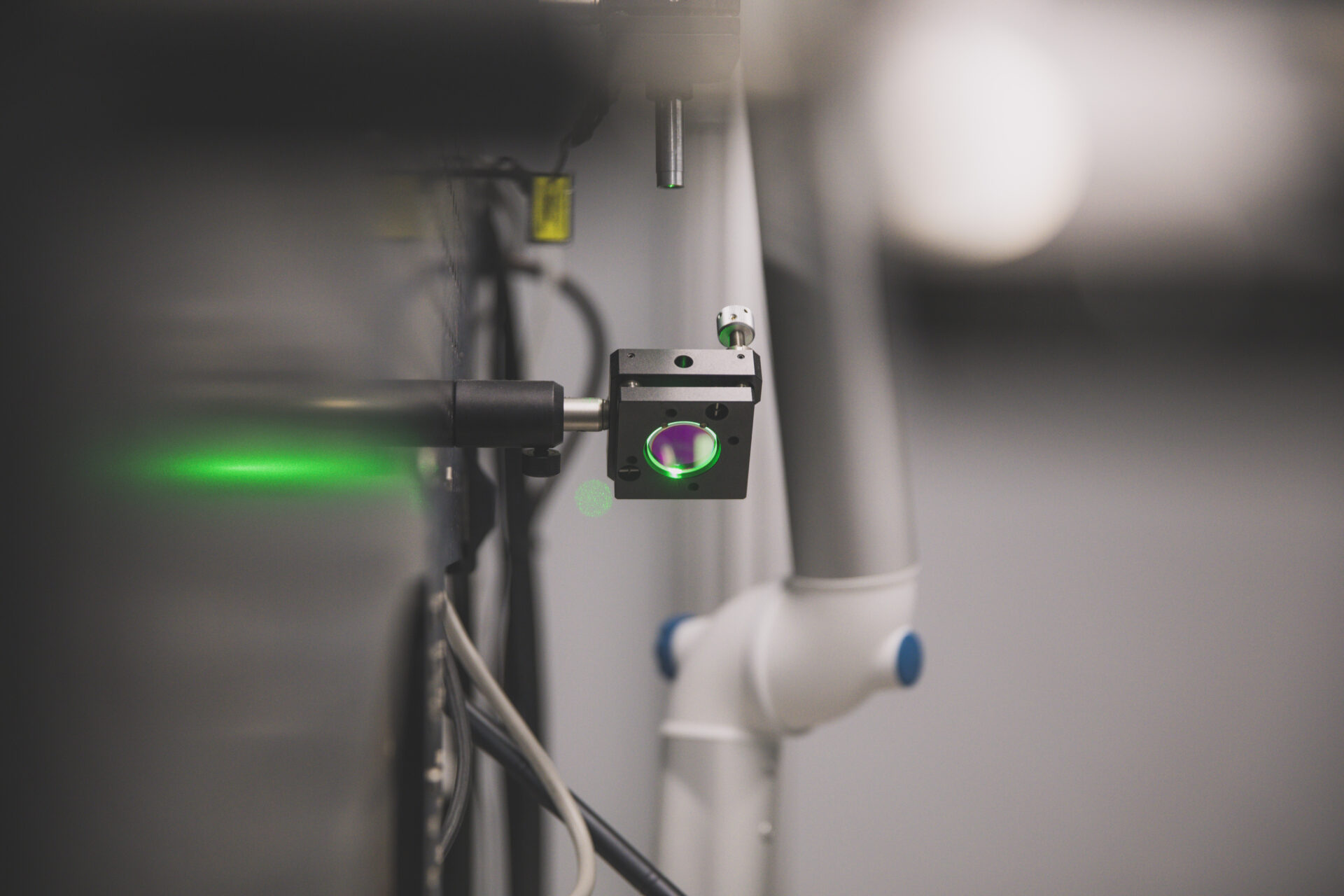
A complete industrial solution
Technical characteristics of our ultra-fast laser processes:
- All materials, from the hardest to the most fragile
- Extreme precision
- Thermal control
- No post-treatment (pre or post)
- Reproducibility
- Large surface geometry: flat 2D and complex 3D
- All part sizes from μm² to m²
- Material removal without burrs or thermal impact
- Dimensional control
Operational characteristics of our ultra-fast laser processes:
- Accelerated productivity
- Cost optimization
- Better end-product performance (the process enhances the intrinsic performance of the material)
- Low-carbon footprint: limited power consumption, non-contact technique, no additives and no consumables
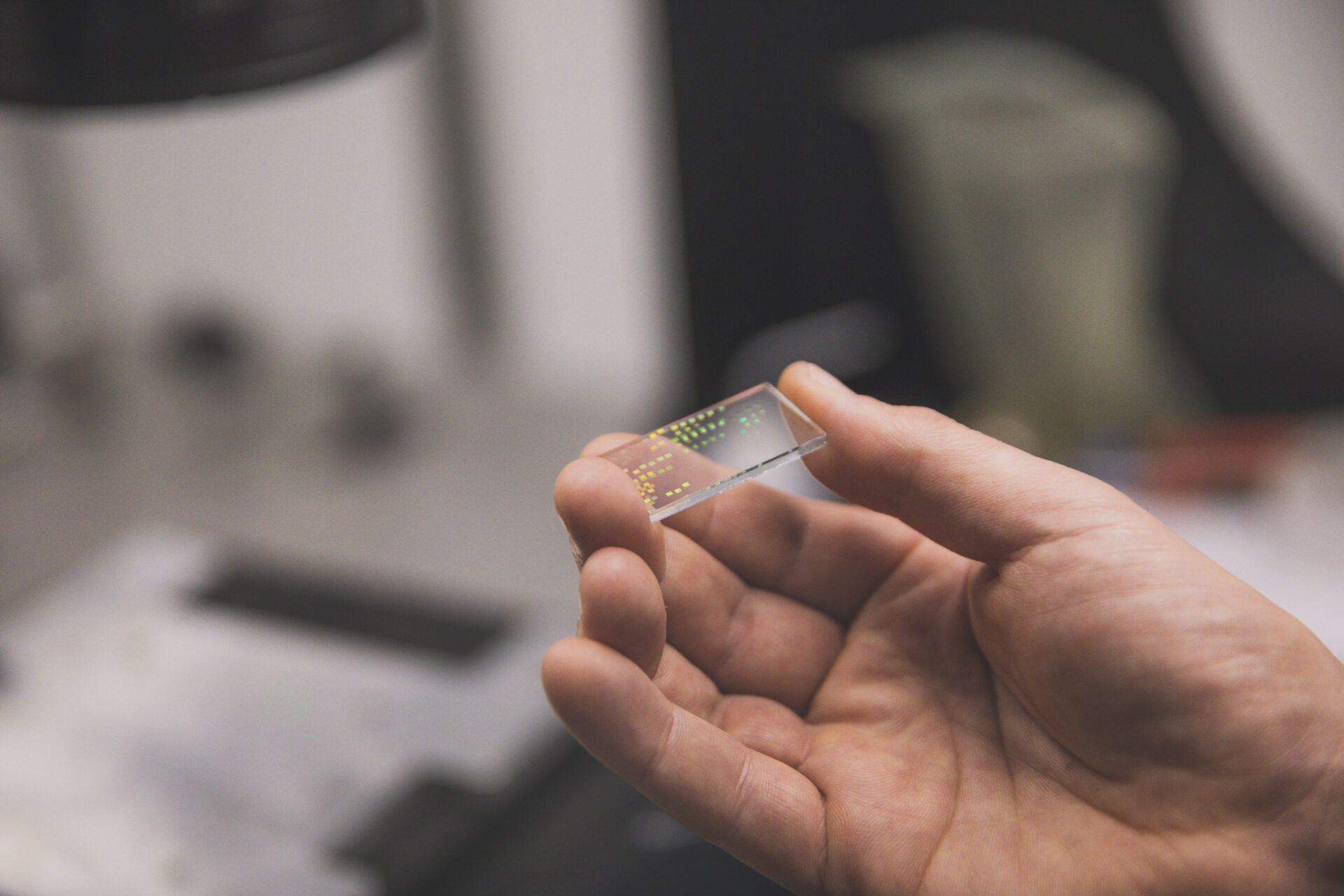
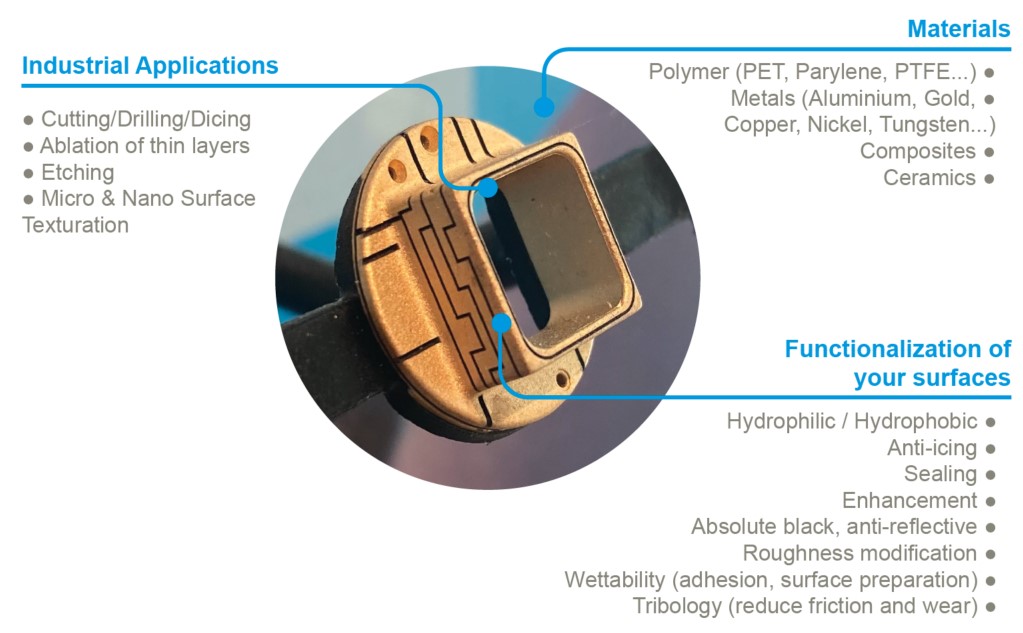
Value chain by HEF
HEF is intrinsically linked to the world of knowledge. Collectively, the men and women at HEF act as the link between the worlds of science, research, and industry.
HEF capabilities
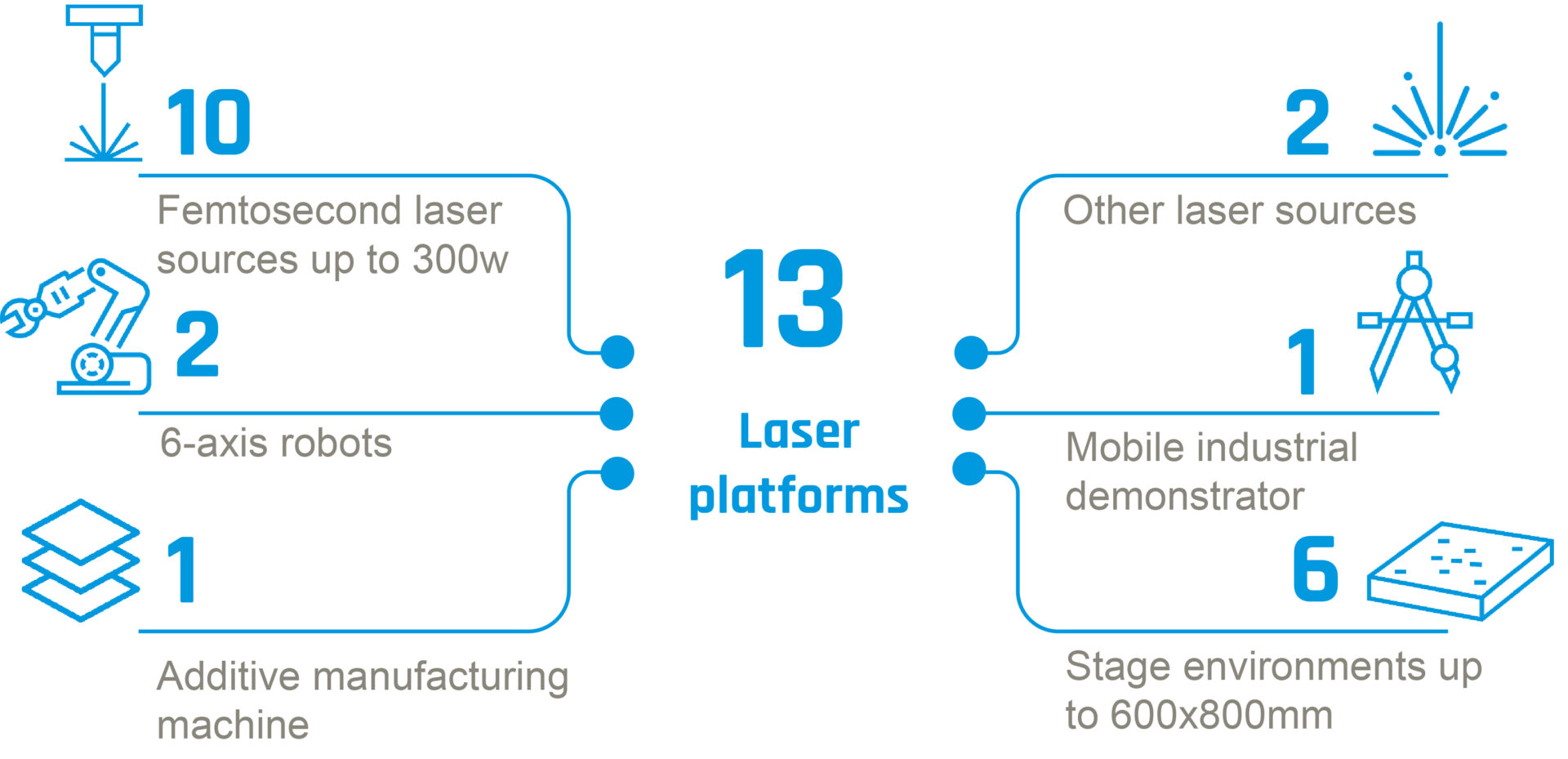
Application: Etching
Femtosecond laser technology enables precision etching with rapid machining (mm³/s) and surface roughness below one μm without damaging the 2D and 3D material.
The femtosecond laser enables etching with thermal control and preservation of material health for microchannel creation, tribology, sealing or aesthetic aspects.
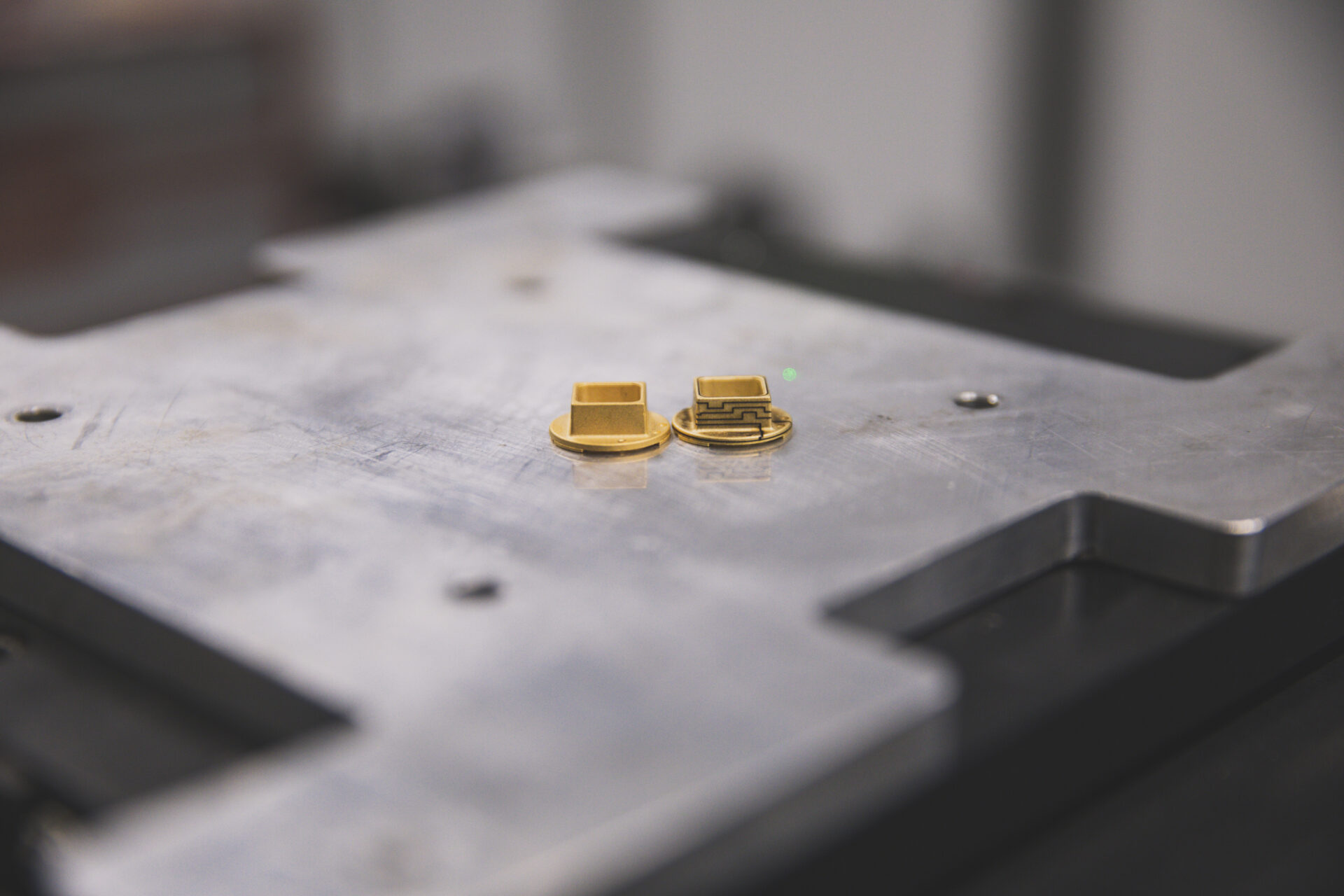
Application: Nano-texturing and micro-texturing using a femtosecond laser
Ultra-fast laser surface texturing can be implemented to modify the structural properties of the material and add technical functionalization to the part.
Femtosecond technology enables texturing through high-speed ablation (mm³/s) at extremely high resolution (μm) without damaging the 2D and 3D material.
Femtosecond lasers can also be used to create nanometric surfaces for various functionalities:
- Wettability (hydrophobic, hydrophilic, etc.)
- Sealing
- Anti-icing
- Tribology (friction, adhesion, chafing, etc.)
- Conductivity
- Color (absolute black, iridescent effect, etc.)
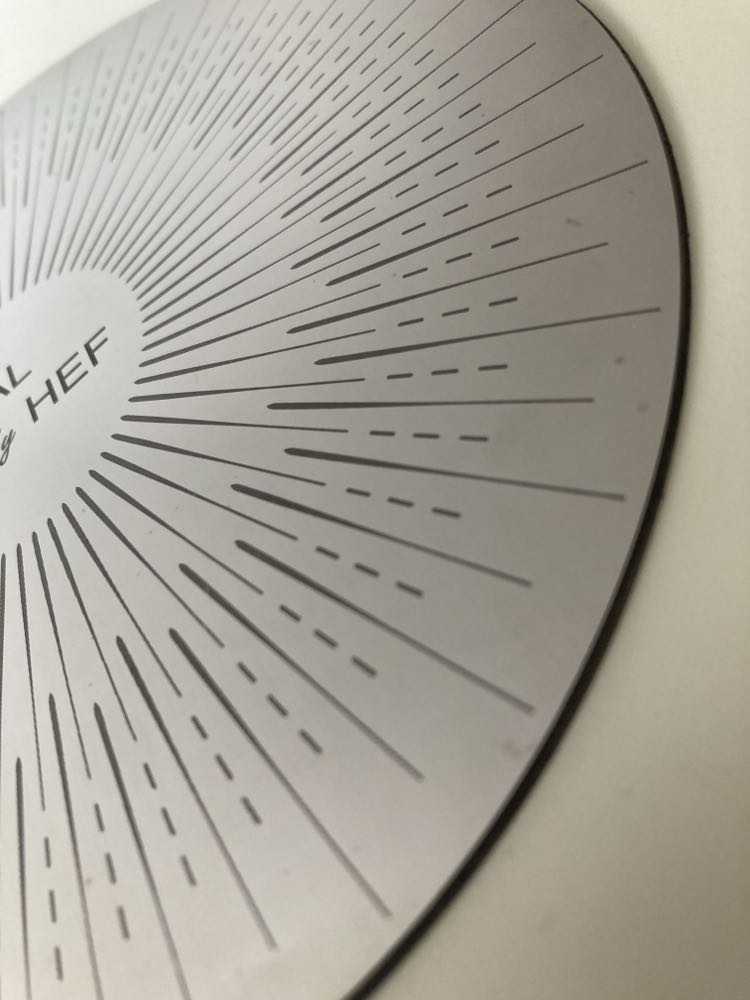
Application: Cutting and drilling
Laser drilling makes it possible to create small holes (as small as 10 µm in diameter) with various geometries for applications on glass, metal or plastic.
Laser technology enables through-cutting of different materials (thickness ≤ 1 mm) at high speed (1 m/s in a straight line and ≥ 0.2 m/s for more complex geometries).
The laser makes it possible to preserve the substrate by controlling the thermal effects and providing clean, burr-free cutting edges.
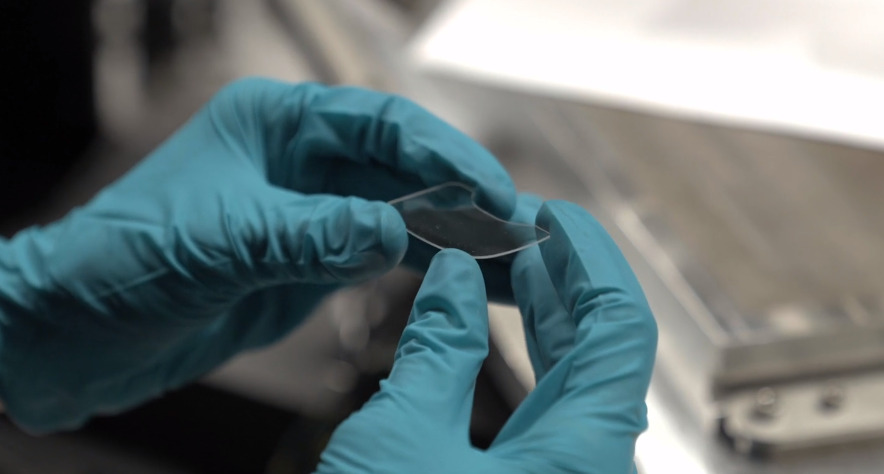
Application: Selective ablation of thin layers
Laser ablation of thin layers (or de-coating) allows selective etching of a layer on its substrate with no delamination, burrs or micro-fissures.
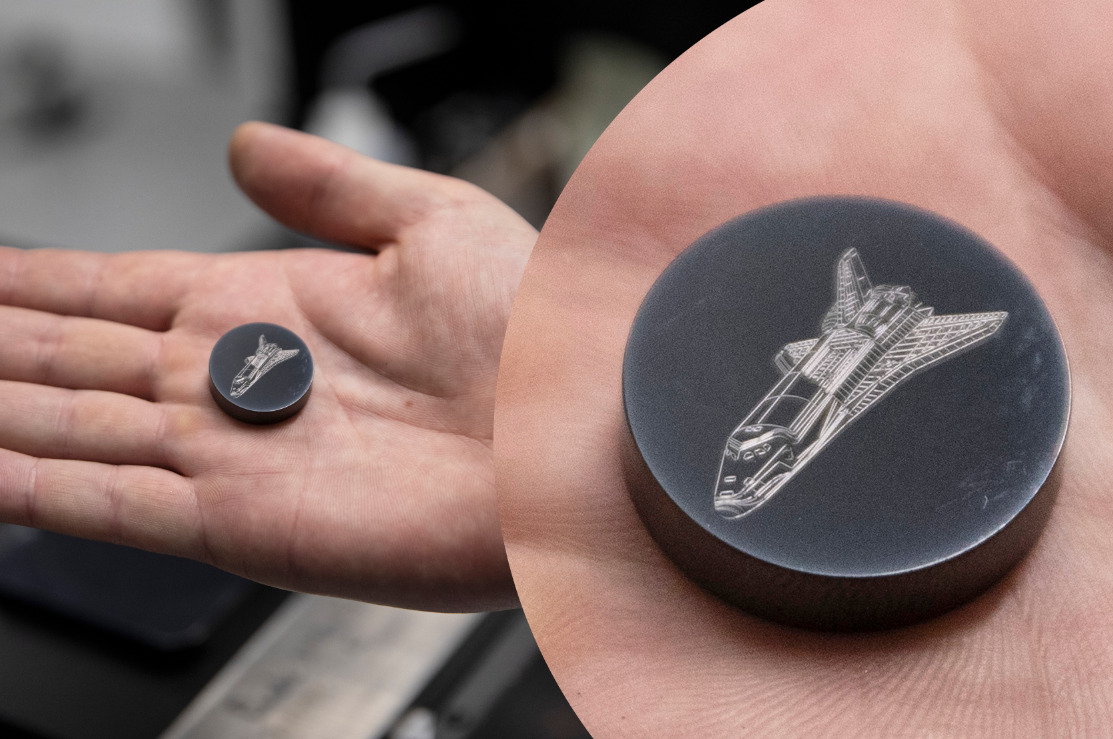
Conclusion
Applications such as femtosecond laser cutting, etching, functionalization or surface texturing are already deployed in the aerospace, defense, energy, and electronics industries.
Biomimicry is one source of inspiration for this technology. For example, we can reproduce the structure of shark skin to improve hydrodynamics, the structure of a lotus leaf to make surfaces hydrophobic, or the structure of gecko legs for adhesion.
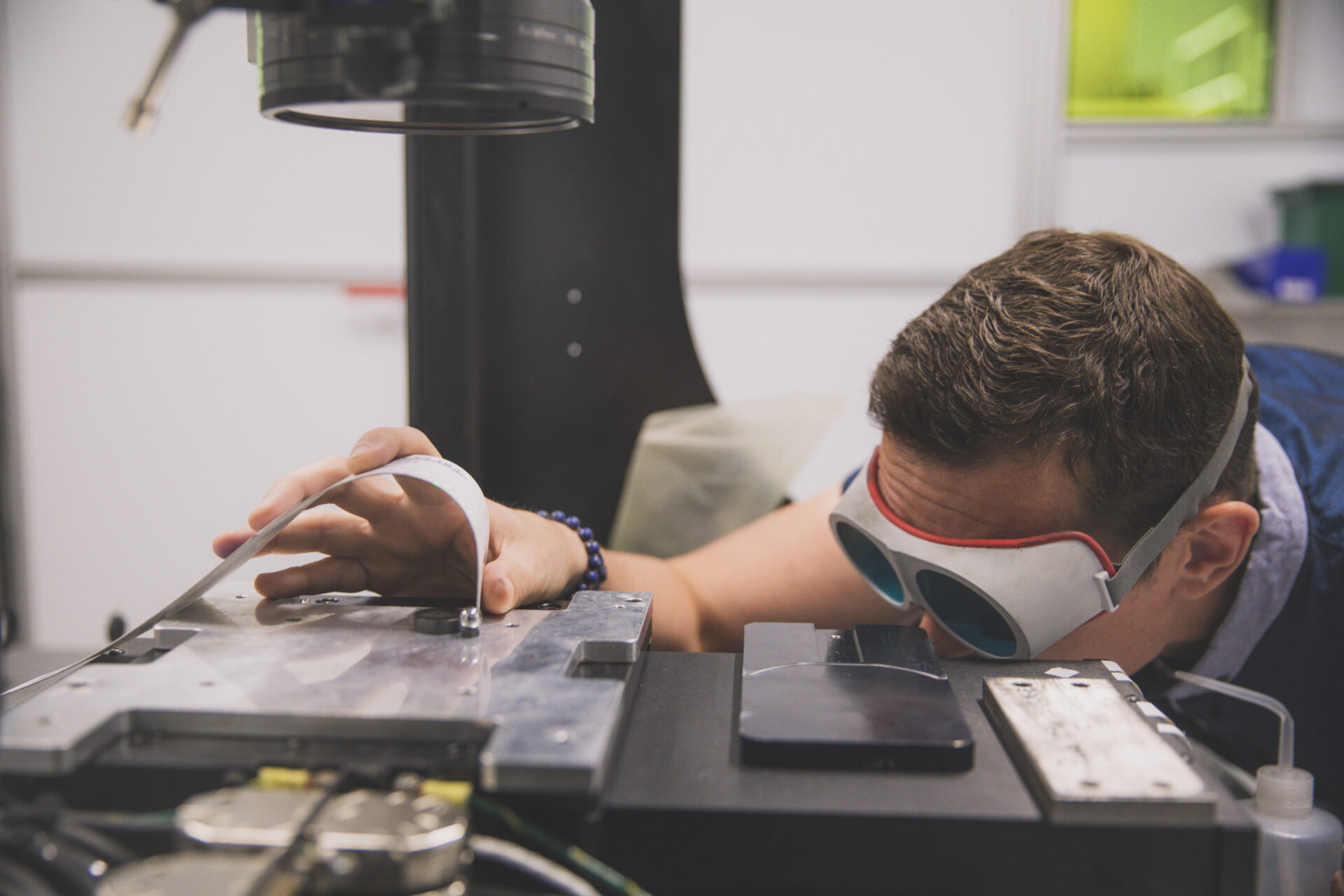