Wind turbines, located in hard-to-reach locations, require costly maintenance, particularly for complex mechanical sub-assemblies. The design of the rotor, consisting of the wind turbine, nose and blades, is based on a shaft rotating in bearings installed in the nacelle. This system, subjected to heavy loads, benefits from our specific surface treatment for wind turbines, including Certess® Carbon DCY and Carbon DT. They considerably improve the system’s service life by offering protection against seizure, reducing the coefficient of friction, ensuring optimal operation, and drastically reducing maintenance costs.
Coatings for Tribological Applications:
Our coatings are made up of several underlayers of different materials: Cr, CrN, WC, WCC, combined with a top layer of amorphous hydrogenated (a-C:H) or non-hydrogenated (ta-C) carbon.
Characteristics:
- Hardness from 500 to 6000 HV
- Excellent friction properties
- No hydrogen embrittlement
- Compliance with dimension and roughness specifications
Materials suitable for treatment: steels and cast irons – carbides – dense sintered materials – Inconel alloys – aluminum, copper and, titanium alloys.
Wind turbines operate in difficult conditions all year round, subject to temperature variations, variable humidity levels, and significant load changes. The H-Liner® range of friction components is particularly recommended for wind turbine applications, such as rotation systems, anchoring (in floating offshore wind turbines), and pitch systems.
Our CLIN™ technology solution provides:
- high resistance to corrosion (400h NSST)
- high resistance to fretting
- good compatibility with seals (O-rings)
- compliance with REACH regulations
In particular, we offer our CLIN™ surface treatments for wind turbine blade drive and braking systems.
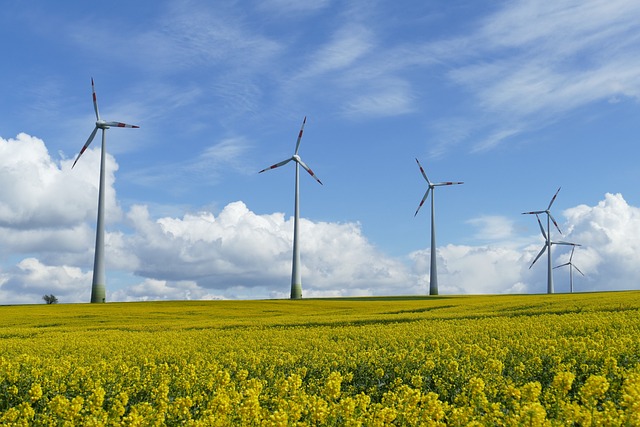
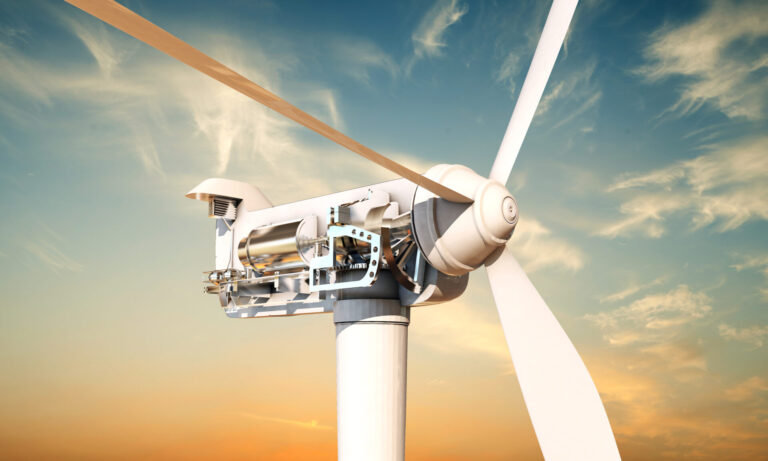