Light-duty vehicles are at the heart of both the industrial revolution and the digital revolution, and are indicative of technological progress as well as the challenges of climate change.
HEF’s CLIN™ technologies are particularly recognized and adopted by leaders in the sector of gas cylinders used in automotive applications (OEM and aftermarket). They offer superior corrosion resistance (>120 hours in salt spray) as well as optimized mechanical and friction properties.
This surface treatment for the automobile industry includes the following applications:
- Shock absorbers
- Differential systems
- Brake systems (disc, pads, brake piston)
On these components, our CLIN™ technology provides different properties ranging from mechanical fatigue resistance to increased corrosion resistance.
HEF’s “Diamond-Like Carbon” (DLC) coating offers incomparable advantages for improving vehicle performance, including a coefficient of friction that is much lower than that of conventional hard coatings such as TiN, CrN, etc. (5 to 10 times lower) allowing the reduction of CO₂emissions.
Our solutions are already being used by engine manufacturers around the world to improve friction in:
- rocker arm systems;
- mobile hitch systems; and
- transmission systems
On the other hand, for electric vehicles, HEF is developing laser texturing solutions to improve the adhesion force on polymer parts subjected to high pull-out forces.
Prevention of electric arcing in e-vehicles is a major issue for automakers and, consequently, a solution for electrical insulation and temperature resistance is in demand. Powder coating technology meets these expectations.
Powder coating is easily and quickly applied on all geometries and sizes of 2D and 3D parts. There are no volatile organic compound (VOC) emissions, and powder coatings provide electrical insulation up to 5000 V and temperature resistance up to 500°C.
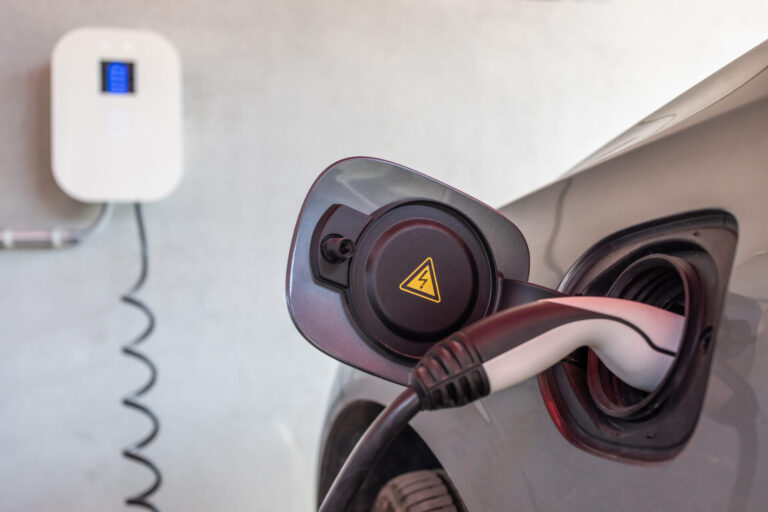
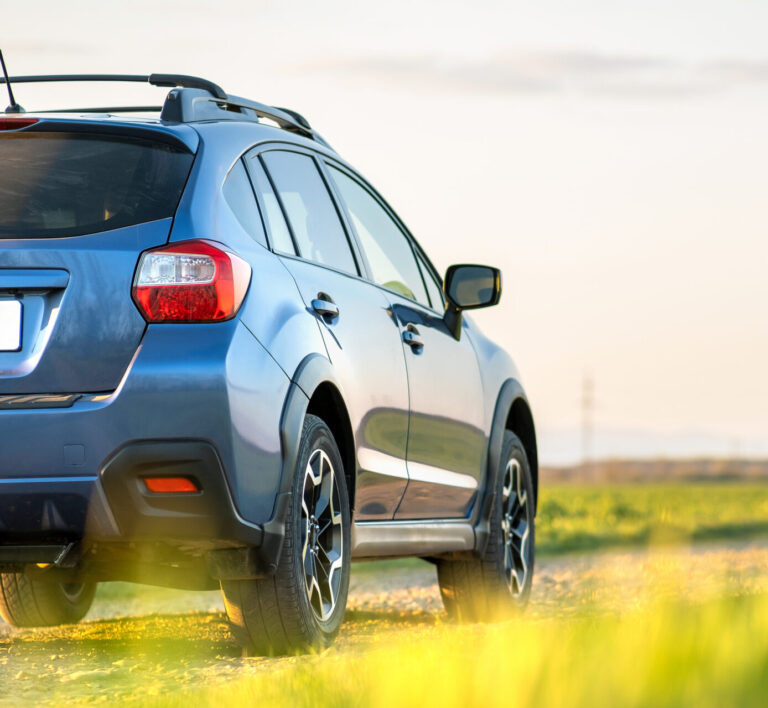