The alternative offering to an electric solution
Although we often consider the solution of batteries when we speak of electric vehicles, this is however not the only technology available, nor is it the technology best suited to all modes and uses of transport.
The mobility market is divided in 2 major poles: personal vehicles and professional vehicles. One of the differences between these two modalities is the rate of vehicle use; in other words the ratio between the real time of vehicle use and the time of total time available.
For personal vehicles, the rate is quite low. On a typical weekday, the vehicle will primarily be used to drive to work and return from work, with a long period of immobility in between. The model, electric with battery, is effectively adapted to this type of use. However, an electric car is still characterized by a recharging period that is quite long, on the order of one hour to half a day, depending on the power provided and the type of vehicle.
In the professional use scenario, you cannot allow a vehicle to be immobilized for a longer period of time. Thus, the battery is not necessarily suitable for this type of use. This is where another electric modality comes in: namely, the fuel cell.
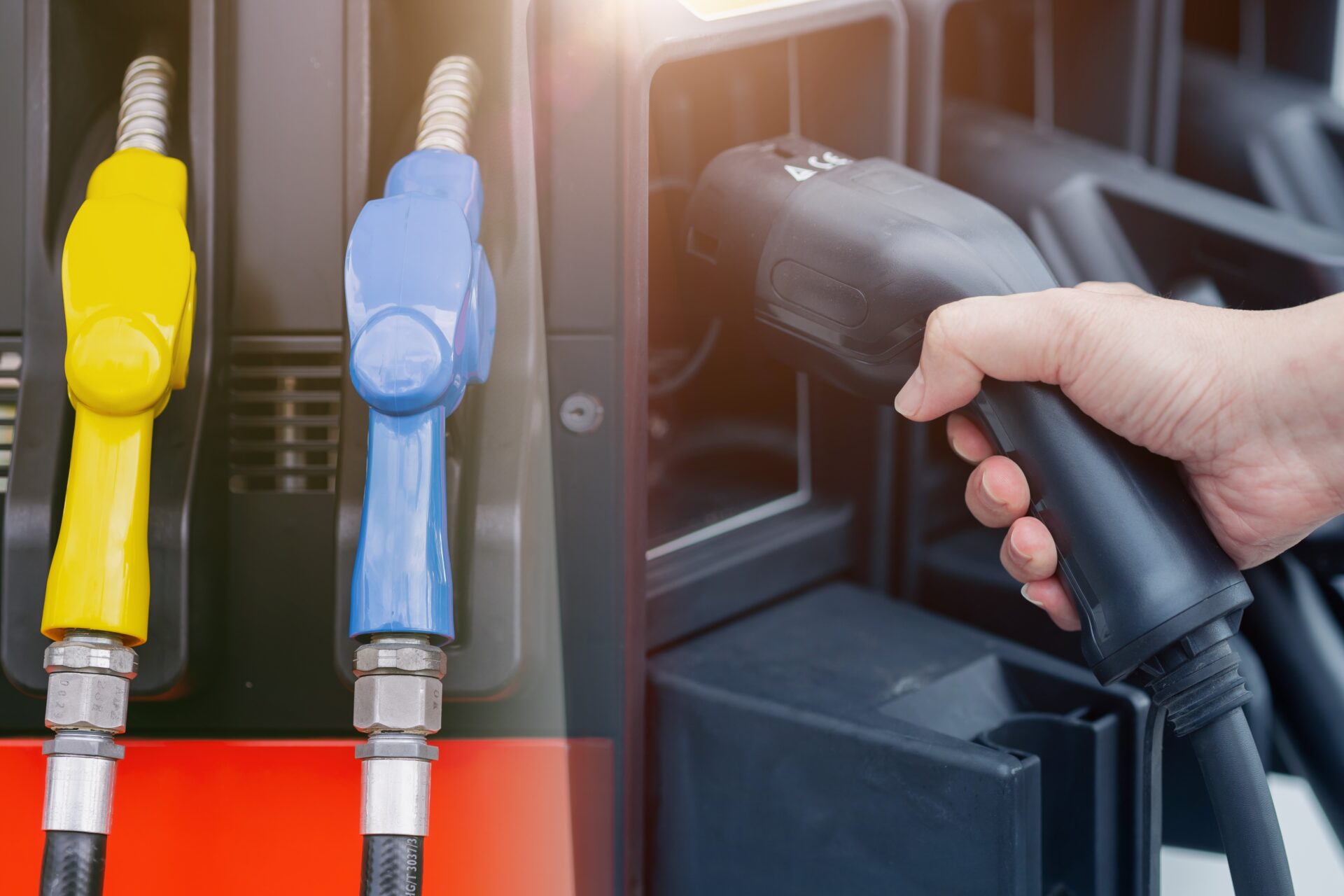
Fuel cell technology
The proton-exchange membrane fuel cell (PEMFC) enables a “low-pressure and low-temperature function”, which in turn makes it possible to integrate these functions in vehicles. Its principle is simple: Inject hydrogen, let it react with air oxygen to transform the chemical energy of this reaction into electrical energy that can be used to propel the vehicle.
Thus, a vehicle equipped with a fuel cell must be regularly full of hydrogen in order to supply this cell. Such a hydrogen recharge is very much faster (several minutes) than a battery recharge. Consequently, it enables a much higher vehicle utilization rate, such that this technology is particularly well-suited to various professional transport vehicles such as taxis, shuttle buses, utility vehicles, vans or heavy-goods transport.
Currently, there are 9 hydrogen service stations that can supply the vehicles equipped with fuel cells in Paris. In 2023 in Europe there were already 254 stations and 37 new stations have opened this year. In 2023 the European Parliament officially adopted new regulations aimed at imposing installation of these hydrogen service stations every 200 km along the major routes of the European Union by the year 2031.
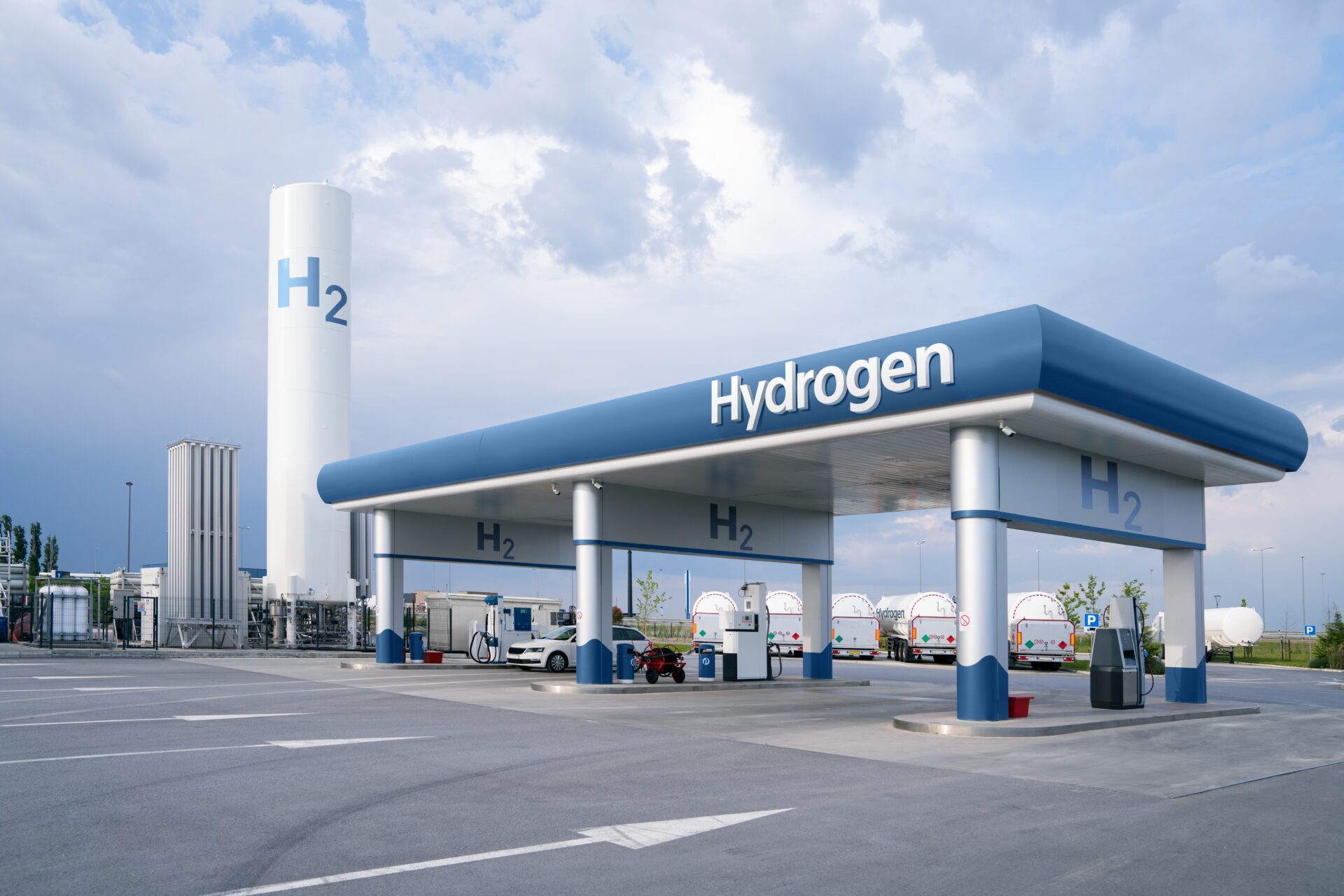
Constant optimization of fuel cell technology
A fuel cell consists of a stack of multiple cells, each stack made up of plates called “bipolars”, which are surrounded by an active milieu where the chemical reaction occurs. The more cells you add, one behind the other, the more you increase the power of the stack.
Historically, the bipolar plates were made of graphite, which is a good current-conducting material and stable in the chemical environment of the stack (i.e. corrosion-resistant). However, this material necessitated making the bipolar plates very dense and heavy. It is the basis of fuel cells that are efficient but quite bulky. Graphite fuel cells are still used today in vehicles where the size of the stack is not an issue, for example the Alstom Coradia hydrogen train in Germany.
For road transport (trucks, cars) stacks that are smaller, more compact, lighter, are required. Consequently, these graphite plates were replaced by stainless steel plates. Advantage: the plates are 10x thinner. Disadvantages: Stainless steel is not stable, nor is not a conductor in the stack environment. This in turn necessitates the use of a gold coating (electrically conductive and chemically inert).
Thus, it became possible to make these stacks more compact, and usable in smaller vehicles.
However, given the use of large gold-coated surfaces in the stack, the problem of price had not been effectively resolved … that is until now.
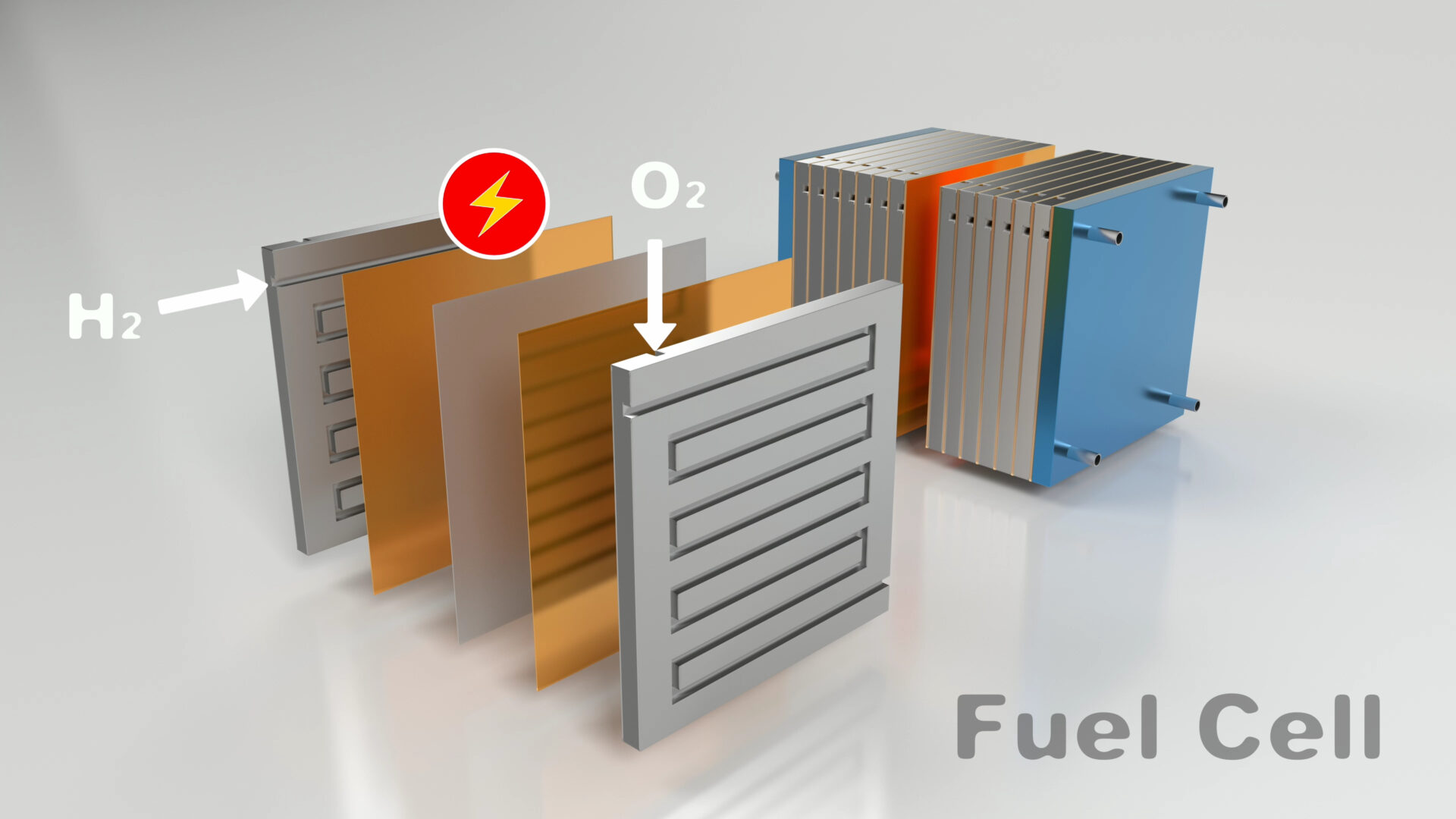
The HEF technology solution
The HEF solution is to replace this gold coating on the bipolar plates with a specific, carbon-based material, for which 3 patents have already been applied for. This involves a thin carbon film deposited by vacuum spraying, and specially designed for good properties between the properties of graphite (excellent conductivity) and the properties of diamonds (chemically inert and excellent mechanical strength). This material does not exist in nature and it must be developed industrially. The name of this process for vacuum pulverization of carbon is: CERTESS (sprayed materials) ELEC (electrical industry) FC (Fuel Cells – dedicated to fuel cells)
HEF’s objectives are not only to develop this material, but also to make it economically competitive. This is accomplished by strategic vertical integration which enables us to develop the specific equipment such that production costs (plus the cost of the material itself) will also be as low as possible.
Consequently, this year HEF transitioned from the R&D phase to the industrialization phase in the Berthiez Halls, 12 000 m² near the city of Saint-Etienne. From now until 2027, this pilot plant will accommodate five production lines, equipped to industrialize this new coating process for the bipolar plates of the fuel cells, with an annual production capacity that can equip 50,000 vehicles per year. Another objective is to reduce the cost of this process by a factor of 10 using classic technologies, in order to make this solution economically competitive.