Patterned Filters: Crucial Elements of Precise and High-Performance Multispectral Imaging
Today, it has become essential to be able to " see " all those colors that the human eye cannot capture, but which contain a wealth of crucial information about the world around us. To do this, humans have built their own artificial " eyes ", capable of scanning the entire spectrum at will.
Often, within this vast range of colors (called ‘wavelengths’), only certain ones are of interest, which will be characteristic of a phenomenon to observe. It then becomes necessary to build filters that only allow the considered wavelength, or a well-defined range of wavelengths, to pass through.
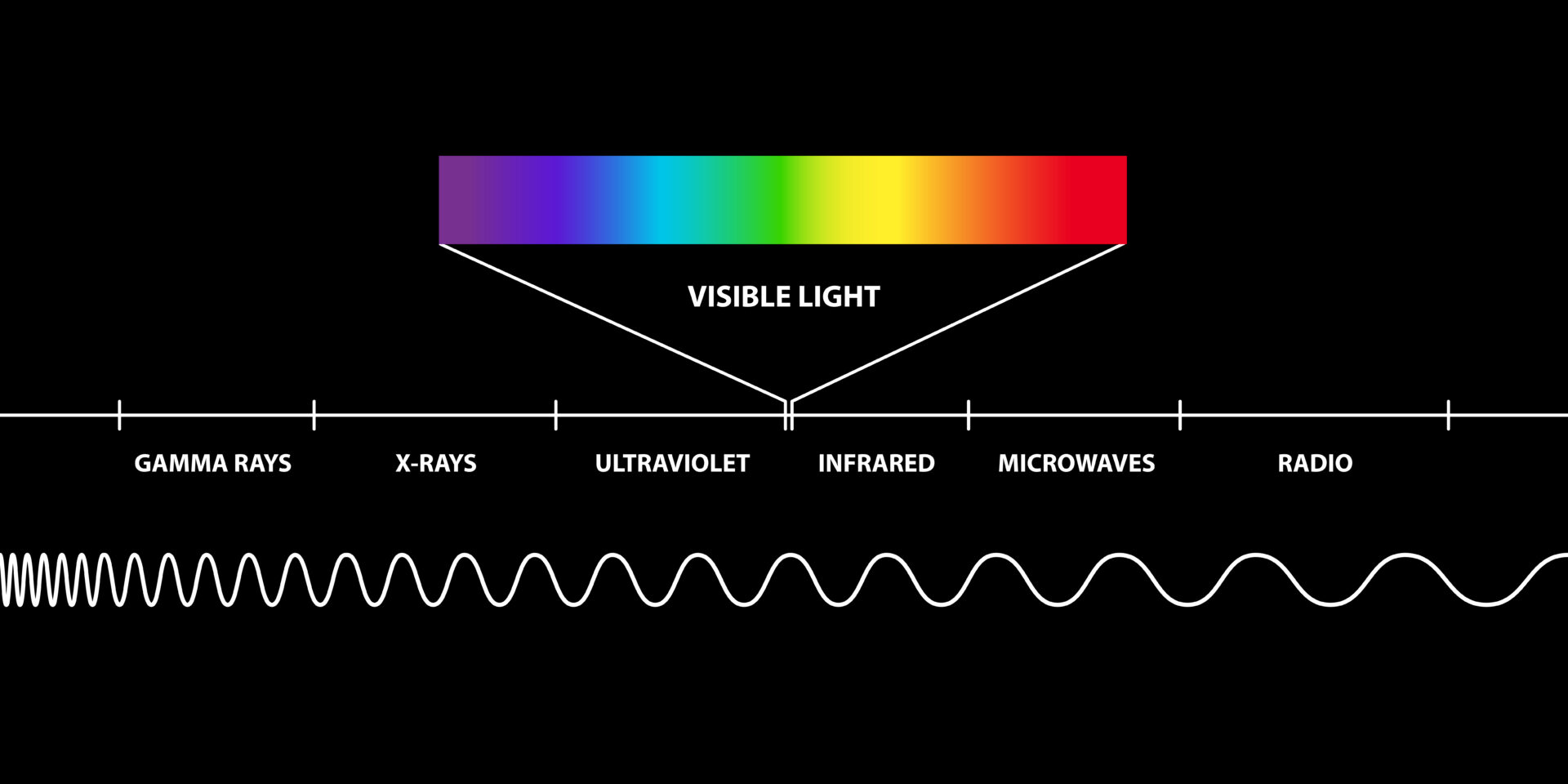
Challenges and Technological Solutions in Environmental Observation via Satellite
These constraints are very present in the space domain. Let’s take, for example, the European Copernicus program for environmental monitoring. It relies on a multitude of satellites, each dedicated to a specific part of studying the Earth’s environment (soil, atmosphere, oceans, polar ice caps, vegetation, climate change).
One of these satellites, Sentinel 5, is tasked with studying air quality and the influence of the gases that compose it (ozone, sulfur dioxide, carbon monoxide, methane…) on climate change.
Each of these gases only emits at very specific wavelengths, on which the satellite’s instruments must be able to adjust in order to observe and study only that particular gas.
Problem: For a given position above the ground, it is necessary to take images of all types of gases simultaneously. However, the satellite is in constant motion above the surface of the planet, traveling at a speed of 27,000 km/h. It is therefore not feasible to take sequential images, changing the filter after each shot, for the risk that the surface observed by the last filter may no longer be the same as the one seen by the first (not to mention the clouds that could pass through the observed field during this time).
Solution: Place in front of the imaging instrument a set of tiny strips of each filter, glued together, each no wider than a pixel, covering the entire sensor.
For Sentinel 5, for example, which works in 7 different wavelength ranges, 7 " matchstick " filters will be placed side by side, and this operation will be repeated across the entire width of the sensor. Thus, in a single image, the same area will be seen through all the necessary filters, and the correspondence will be perfect.
Certainly, in the end, only part of the sensor is dedicated to each filter, but modern instruments have more than enough pixels so that a small portion of the total surface is enough to create a perfectly usable image.
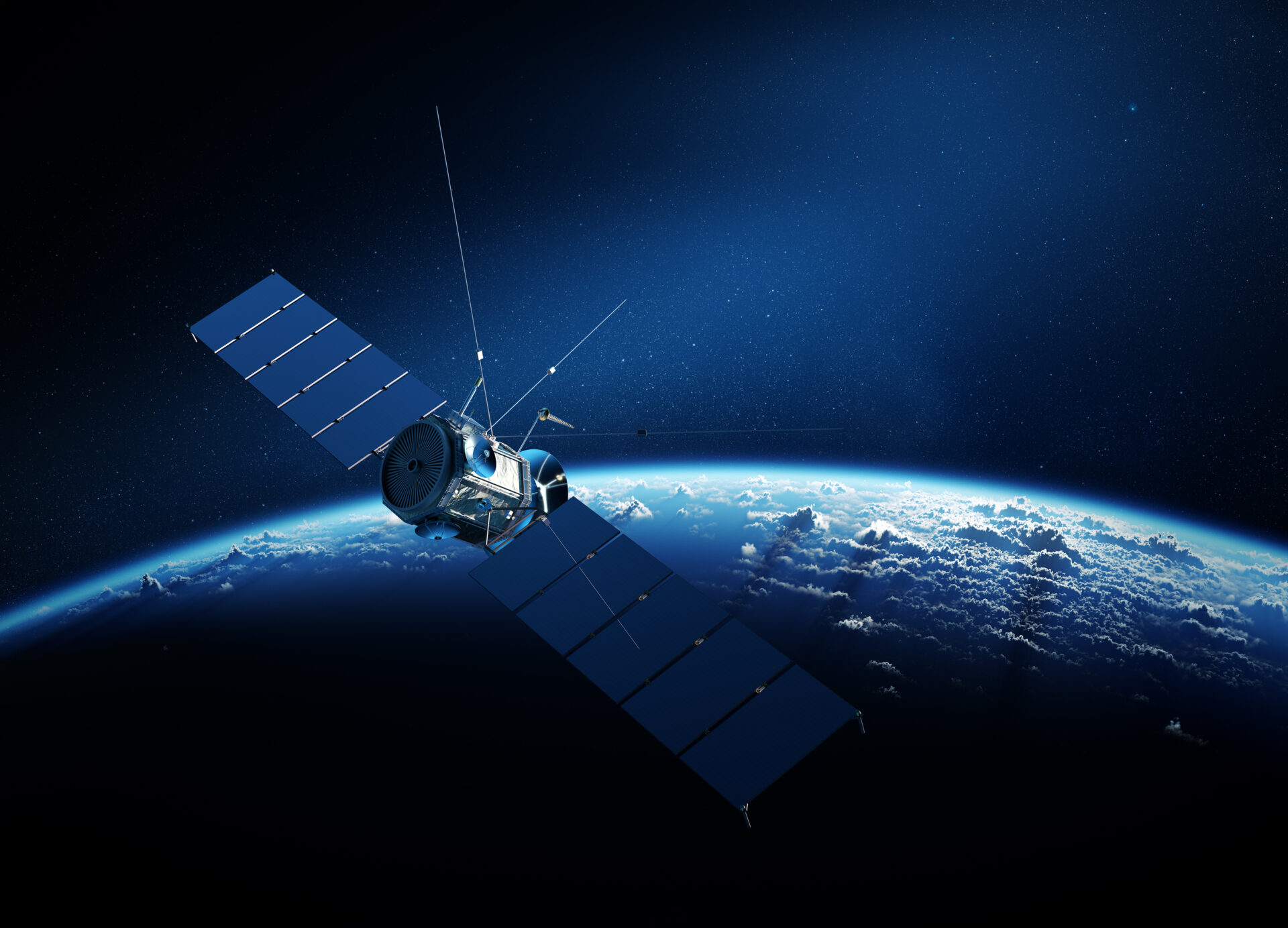
The Technical Challenges of Manufacturing Filters for Space
Transitioning from theory to practice represents a significant challenge for several reasons.
First of all, these filters are meant to be used in space, one of the most hostile environments for materials. Manufacturing filters exposed permanently to temperature variations of nearly 150°C between shadow and sunlight, to the vacuum, and to the constant irradiation from cosmic rays and other ultraviolet radiation requires great expertise.
Next, as sensor technology continuously evolves, pixels are becoming smaller and more numerous. It is increasingly difficult to etch and glue together strips of filters that are only a few microns wide and several centimeters long, and to certify their quality and uniformity.
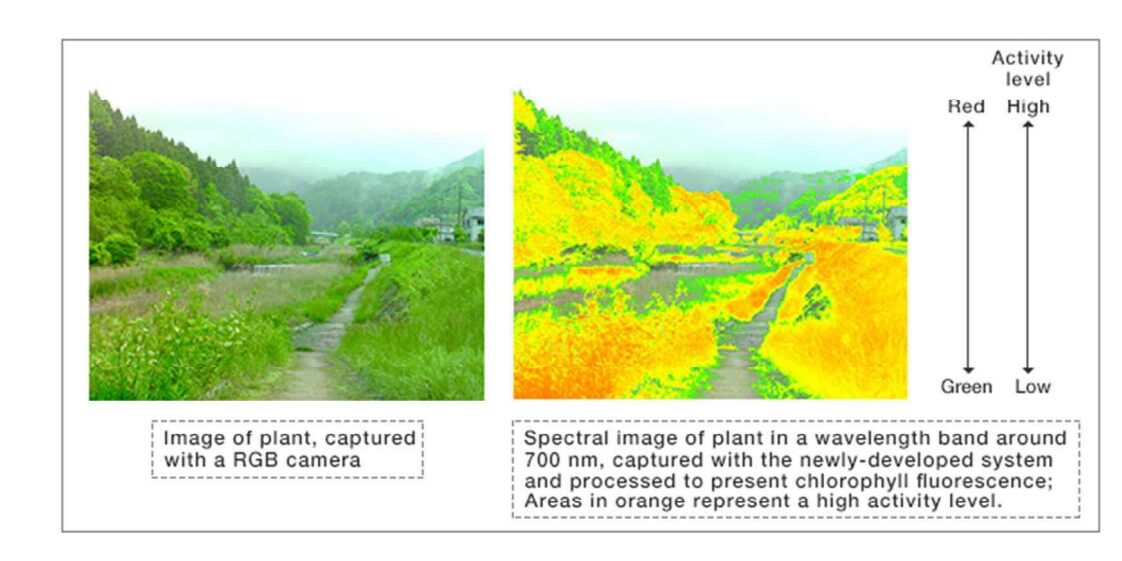
Manufacturing Patterned Filters for Space: Micrometer-Level Precision
To make these so-called " patterned " (or " matchstick ") filters, we use a glass structuring technique. The surface is coated with resin, except for the thin strip where we want to place the intended filter. This filter is actually made up of more than a hundred layers of materials (metal oxides) with perfectly controlled optical properties, which will be deposited using " ion-assisted evaporation, " a technique that HEF masters very well. Once these successive layers are deposited, only the desired wavelengths of light pass through this stack to the sensor.
The resin is then removed, and another layer of resin is deposited again, with an opening just next to it, where we want to place a new strip of a different filter, and so on until the entire glass surface is covered with micrometer-level precision.
Once this glass surface is completely covered with a large number of parallel " matchstick " filter strips, an absorbing layer will be applied between these strips to prevent light passing through one filter from spilling over onto the neighboring one. The finished product can then be deposited as a whole onto the sensor for final assembly.
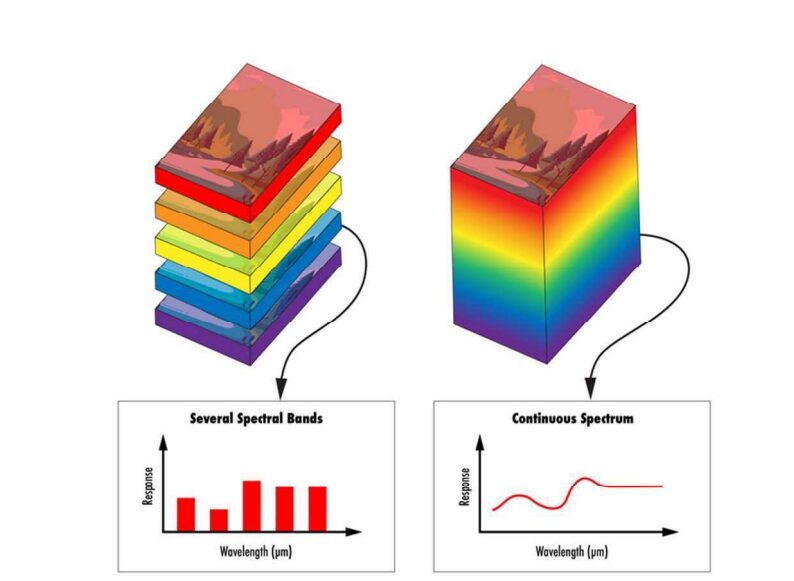
From Design to Production
The specificity of HEF in this entire thin-film ‘matchstick’ filter deposition process is that we control all the technologies and processes in the same place. The entire operation chain is fully controlled by us, ensuring a high-quality final product.
HEF collaborates with institutions to develop cutting-edge technologies that can be used in the next generations of satellites..
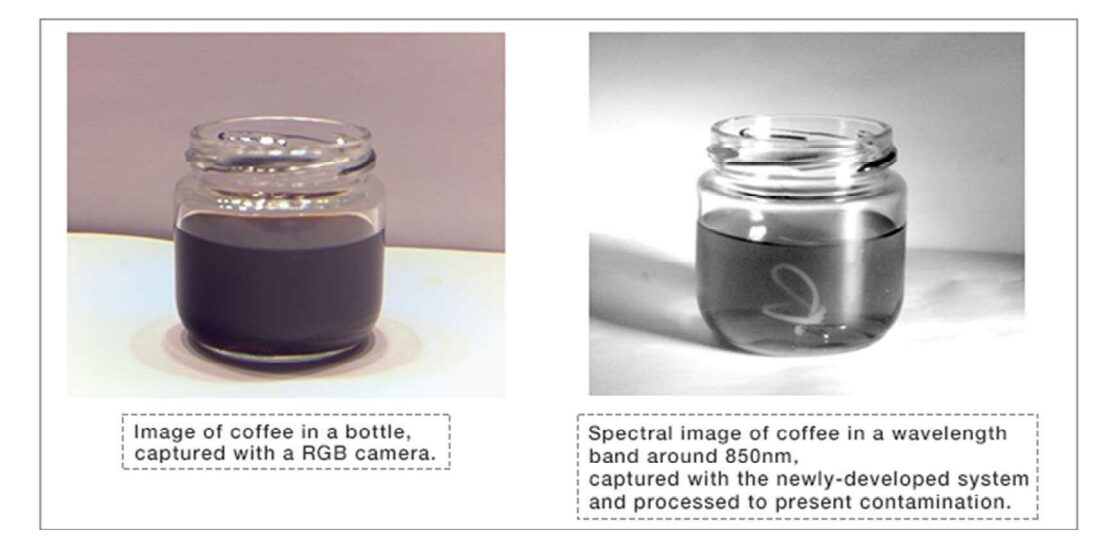